One of the key milestones in a project's timeline is the opening of the site location. As a supervisor, you'll ensure all the cogs of the wheel turn in harmony, and if anything gets stuck, you'll be the grease that keeps everything running smoothly.
Let's start this topic with an activity confirming some of the information we have learned.
Monitoring progress
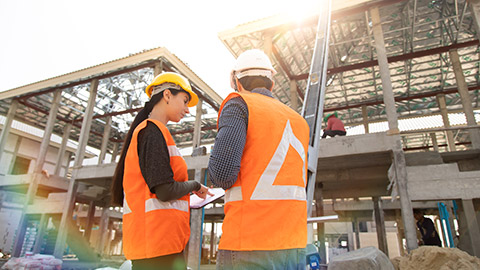
As we've discussed before, the project schedule outlines all the tasks needed to complete the work. By regularly comparing and documenting the progress and completion of tasks to the planned timeline, we can see how efficiently work is being done, providing a clear picture of the current progress. Documentation allows for analysis of the issue later so procedural changes can be considered that keep the business operating efficiently.
When managing project progress, always set and communicate expectations and objectives so everyone on the project knows what they are working towards. It also helps to regularly check in on everyone’s progress towards the goals so any issues can be addressed as they come up.
Be sure to review your organisation’s policies and procedures for monitoring project progress. This process is typically done by holding meetings and asking workers in charge of particular areas about the status of their work's progress.
When the timeline of a project has to pivot around an unforeseen event, there are usually personnel considerations to the issue. When you are communicating about these situations, it will help to know that worker productivity refers to the output per hour of labour. The output may then be expressed in terms of units of product or value of construction.
The factors that would affect this productivity could include:
- the age, skills, and experience of workers
- the complexity of the project
- inefficient utilisation of equipment
- absences due to accidents, illness, or family matters
- strikes
- site climate unsafe for work
- other unforeseen work stoppages.
Resolve issues within the scope of responsibility
Dealing with various problems throughout the application of the project is one of the primary roles of project supervision. Supervisors must have a clear understanding of their responsibilities to manage these unforeseen circumstances with the least amount of impact (time and money) on the project.
As a commercial site supervisor, you will receive issues communicated by your employees, subcontractors, clients, and your vendors. It is also crucial to proactively identify potential problems by closely monitoring all project team progress. This involves working closely with your team and all other subcontractors needed while assessing the overall environment around the worksite.
To effectively manage the required budget, regularly check in and compare the estimated costs to the actual expenses of the project. This financial awareness helps ensure budget adherence and assess the project's profitability, which is essential for your company in the commercial construction sector you are building in.
Some issues will be communicated to you by employees, subcontractors, clients, and vendors. Others you'll need to discover before they worsen by monitoring the project's progress. This involves collaborating with both employees and subcontractors, while also evaluating the overall environment around the worksite.
Cost analysis helps predict how well the budget is being managed and determines the project's profitability. This involves monitoring the actual spending on the project and comparing it against the estimated costs documented in its budget.
As one of the site supervisors, you would be the person responsible for coordinating the project schedule, it is your responsibility to resolve issues that may affect the project's progress when you are there. The complexity of the work makes conflicts and disputes a common occurrence in the construction process.
General responsibility at this level includes supplier issues regarding building materials and equipment delivery and human resource issues regarding expected labour delivery.
Another frequent issue is disagreements between parties, such as general site workers, owners, architects, and subcontractors because of varying opinions and interpretations on how tasks are approached and executed.
Essentially, on-site building work is an intricate process that requires the communication and cooperation of multiple stakeholders.
In addition to the few ideas we've provided already, can you think about what other sorts of issues may arise on-site? Check your list against ours.
- unanticipated site conditions
- misunderstanding in contract agreements
- compensation disputes
- fundamental changes in the contract
- different ways of doing things
- cultural misunderstandings.
Worksite evaluation
You'll need to pay attention to informal conversations and feedback, but remember to use selective listening to filter out comments that are just venting. Sometimes, these grievances will point to procedural changes you can implement. Other times, as you gain more experience in the field, you will recognise that certain issues are simply inherent to the nature of the work. Your judgment on these matters will improve as you encounter them more frequently.
Always keep in mind that your response to issues affects the outcome—try not to make things worse. If that does happen, be kind to yourself when reflecting on it. Think about what changes you could have made in your response to lessen the negative effects of the original issue.
Inspections
When the site opens, as the supervisor, you'll be charged with ensuring the project schedule is being met, the materials are being delivered intact and on time, the waste management is all in place, and the people on-site all know what to do and how to accomplish their tasks.
As the deliveries roll in, your inspections will need to get started.
Checking delivered materials
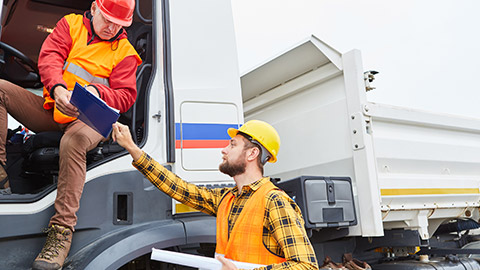
Once the procured building materials have been delivered to the site, they must be checked against the standards and requirements specified in the project specifications. A more detailed inspection of the delivered materials and products can be done when the materials have been stored and when time permits. However, it is essential that as the procured materials arrive, they are spot-checked.
One way of assuring that the materials delivered are adequately checked is by using a delivery sheet. As a supervisor, you either assign a point person or be the one who will be in charge of receiving deliveries, noting their condition and completeness into a record.
Whoever will receive the deliveries must be briefed about the procedures for receiving and inspecting deliveries from the supplier.
Here are some simple steps to check delivered materials once they arrive on-site:
Inspection Process
All materials delivered on-site must be fit for use in construction. It is the supervisor’s responsibility to make sure that the materials are free of defects and are standard-compliant before use.
Checking for defects
Materials must be examined for any naturally occurring and manufactured defects before installation. As soon as the materials arrive on-site, inspect them for any damages that may have occurred before or during transportation. Visual inspection procedures are usually appropriate for initial material checks.
If the materials are found to be defective and the extent of damage renders the materials unusable, the materials should be sent back to the supplier for replacement. However, if the defect is minor and does not compromise the function of the material, you may choose to record this and relay the information to the supplier and see if you can find a fair resolution when time permits.
Comparison with specifications and standards
Materials must also be examined to check whether they meet contract document specifications and quality standards.
For reference, you need to look at the documents that serve as evidence of the suitability of the materials. For example, for steel materials, the supervisor may look at the Mill Test Certificate (MTC) or Mill Test Report (MTR) issued by the manufacturer and compare the details with the requirement.
MTCs and MTRs provide information on the properties of a product and its compliance with the technical specifications. They may also indicate the results of appropriate testing done on a product before it was delivered on-site.
Some inspection activities would also require relevant testing procedures to be done to properly assess the quality of the material. Checklists would often have items referring to testing procedures for materials. Thus, you must also be familiar with various material testing procedures. These tests quantitatively determine whether a certain material meets the standard requirements. Different tests apply to different materials.
Here are common testing procedures for different construction materials:
Material | Tests | Assessing for |
---|---|---|
Bricks | Compressive Strength Test | Compressive strength |
Water Absorption Test | Water absorption | |
Efflorescence Test | Presence of alkalis | |
Hardness Test | Hardness | |
Size, Shape and Colour Test | Uniformity | |
Soundness Test | Soundness | |
Structure Test | Brick structure | |
Concrete | Slump Test | Consistency |
Concrete Cylinder/Cube Test | Compressive strength | |
Rebound Hammer Test | Compressive strength | |
Penetration Test | Compressive strength | |
Pull Out Test | Compressive strength | |
Ultrasonic Pulse Velocity (UPV) Test | Compressive strength | |
Sand | Bulking test | Increase in volume due to moisture |
Silt test | Cleanliness of sand sample | |
Steel | Tensile strength test | Tensile strength |
Brinell Hardness Test | Hardness | |
Radiographic testing | Cracks and defects | |
Ultrasonic Testing | Cracks and defects | |
Timber | Oven dry testing | Moisture content |
Moisture meter | Moisture content |
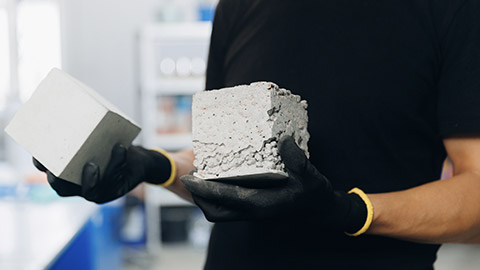
This man is performing a compressive strength test.
Variations and changes to the plan
Variations to the construction plan, drawings, and specifications may occur as the project progresses. These changes are almost inevitable; however, in most cases, these variations are done to benefit the project as a whole.
The term variation refers to when a change must be made to what was previously agreed on in the contract. An example of a variation is when a client requests a change to the design or for a different building material to be used.
When a variation is deemed necessary, management must proceed with the changes procedurally—in a way that relates to or is in accordance with an established or official way of doing something.
This formal approach is an essential practice in the building and construction industry. For one, the documentation of the changes allows better analysis of the changes and, most importantly, permits the variations to be communicated between parties and mutually agreed upon.
Delays must also be recorded and communicated between parties as a delay in one part of the building project may delay the project as a whole.
Variations can come up because:
- of miscommunication
- contract details were misunderstood
- the client decided to add, omit or change the features or specs of the house
- the contract was signed without being thoroughly checked beforehand.
The additional expenses due to a variation must be accounted for. This is crucial in cost planning, as this can affect projected costs. The costs of labour, materials, and other expenses must be identified to document the project variation.
To document variations, you may like to use a form like this example from the fictional company, Clever Kiwi Building:
Download this template in MS Word.
Remember to look to your organisation's standard practices for documenting variation—it may be simpler than this form implies.
Activities
Quiz recap
Let's review some of what we've just learned with this five-question quiz:
Case Study - Roofing materials delay communications
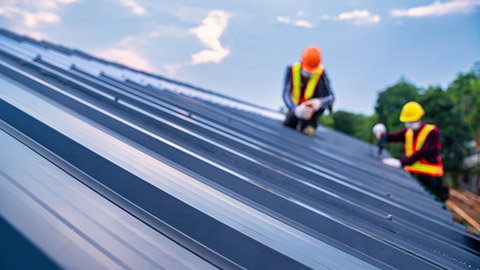
Imagine that you are the site supervisor for a commercial construction project.
Due to unforeseen road closures, the delivery of roofing materials has been delayed, impacting the project timeline. Your task is to communicate this delay to various stakeholders with all the necessary details.
At this point you are grateful that you attend a weekly status meeting, so you can ensure that stakeholders and other personnel are aware of the current status of all aspects of the build — you know it won't be too long before the information about the delay is communicated widely.
That said, you decide some specific information should be provided immediately in a brief email to each of the roles below.
Think about who needs to know what as you complete this activity.
Health and safety quiz
As the supervisor on-site, the safety of everyone must be taken seriously, and plans must be put in place to ensure compliance with protective legislation. The following activity gives you a chance to brush up on your understanding of this important aspect of supervision.
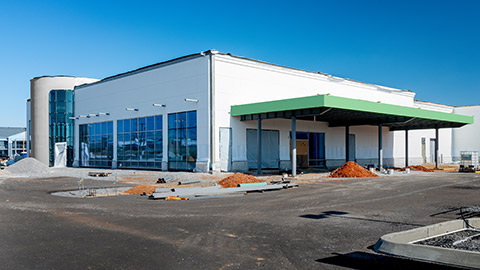
Imagine you have successfully navigated setting up the project schedule, managed the materials, labour, environmental factors, and the build is nearly ready to call complete. These are the final bits and pieces you need to do to ensure you are compliant throughout the entire process before handing the building 'keys' to the client.
Before handing over any finished building or structure, you need to be certain to communicate with relevant company personnel as well as the client that the requirements agreed upon in the contract are fulfilled.
In doing so, contract issues, especially any breaches in the stated original contract can be managed appropriately and with transparency.
Financial requirements
Make sure that the people involved with making contractually obligated payments for the project have been settled.
This may include:
- settling progress payments with clients
- ensure outstanding invoices are processed and paid (e.g., additional inspections, development contributions)
- resolving payment and other financial disputes
- ensuring that all payments have been made to contractors and subcontractors
- ensuring that all financial requirements defined in the contract have been fulfilled.
Legal requirements
Most contracts require compliance with legal requirements and the regulations stipulated in the National Building Act. It is important to ensure that both the building and the construction work adhere to the laws and regulations set by the relevant national regulatory bodies and local Building Consent Authorities (BCA). In other words, you likely did this at the beginning of the project, but check again just to be sure.
Some of the legal obligations to consider include the following:
- The Building Code itself
- Building Consent obligations
- Resource Management Act 1991
- Fire Service Act 1975 (if appropriate)
- Health and Safety at Work Act 2015.
- Local Government Bylaws: Local councils may have additional bylaws and regulations that apply to building and construction activities within their jurisdiction. These may include requirements for noise control, parking, and site management.
- Quality Assurance: Depending on the scale and complexity of the project, you may need to implement a quality assurance system to ensure that the building work meets the required government standards.
- Insurance: It's good practice to have appropriate insurance coverage for your building project, including public liability insurance and contract works insurance for the building itself.
- Environmental Impact: The construction project should also abide by environmental regulations, making sure that processes involved in the project promote the preservation and sustainability of the environment. For example, ensure that construction wastes are properly disposed of according to environmental and waste regulations.
Note: For more detailed information on any of these requirements, seek advice from managers, industry officers, or building professionals regarding specific concerns related to your project's laws and regulations.
Notice of practical completion
An important aspect of the contract that can confirm if requirements are fulfilled is the contract’s practical completion statement.
In general, a building project may be considered practically complete when the required building work has been completed under the stated contract, plans, and specifications. At this point, if there are any defects identified, they should only be minor.
The building, as a result, can be reasonably used or occupied for its intended purpose, even with the presence of defects depending on the nature and extent of the defects.
Remember, it is generally not advisable to occupy a building with significant defects that could affect health, safety, or the structural integrity of the building.
The project’s practical completion should be defined in detail in the contract and is one of the requirements that should be reviewed if it is being met. Take note, though, that conditions for practical conditions may vary, depending on many factors, such as the type of contract used and client preferences.
A project's practical completion statements are a key component of the contract and, by extension, the project. It provides the specific criteria for a project to be considered ready for handover. When these criteria are specific, you can easily review the conditions for practical completion when the building is near completion, identify which conditions have been achieved and focus more on those that are yet to be achieved. In doing this, you are already confirming which contract requirements are being (or yet to be) fulfilled.
Practical completion certificate
To be able to confirm if practical completion has been achieved, the contract usually requires inspections to be made as soon as the contractor has deemed the construction as practically complete. A practical completion inspection (PCI) assesses how the building has been constructed. It ensures the following:
- The building is safe to use or occupy.
- It is built following the Building Code, as well as other relevant New Zealand standards
- The building is constructed in compliance with relevant building laws and BCA regulations.
Quiz refresher
See how you do answering these three questions about managing the end of a project.
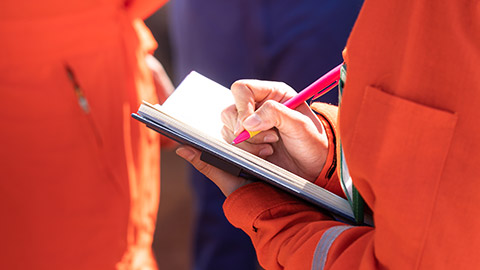
We all learn by experience, and in this section, we'll give you a chance to take on a supervisor role to determine what you would do to keep the project on time, within budget, and compliant. If necessary, you can brush up on areas where there are gaps in your learning by reviewing the content in previous modules before attempting to complete the final assessments.
Branching scenario activity
Enjoy the following activity to get your mind thinking like a supervisor. You'll get a chance to consider what you would do about a:
- material delivery delay
- labour shortage
- dispute between workers.
Keeping your knowledge up to date
We've provided many resources throughout this course so you should have a list of bookmarked websites to ensure you are using the latest standards, guidelines, requirements, and legislation.
Here is a short list of resources to get you started, or to add to your growing list.
- Standards New Zealand
- NZCIC Design Guideline Update
- BIM Handbook
- Stay on top of the latest updates to the BIM Handbook
- Updates to changes to the building code
- Use the References section of this Topic to add to your saved resources.
That's all the knowledge content for this module. Good luck with your assessments and on the worksite!
That's the end of module 13. Let's hear a summary of what we've covered so far.
Click ‘Video Transcript’ or the plus icon (+) to expand and reveal the transcript for the previous video.
Congrats on completing this module. We have identified how the skills in sourcing information, staying relevant to your sector and collecting experiences through the examples of project scenarios can help you become a better supervisor. Well done on reaching this far. Give yourself a pat on the back.
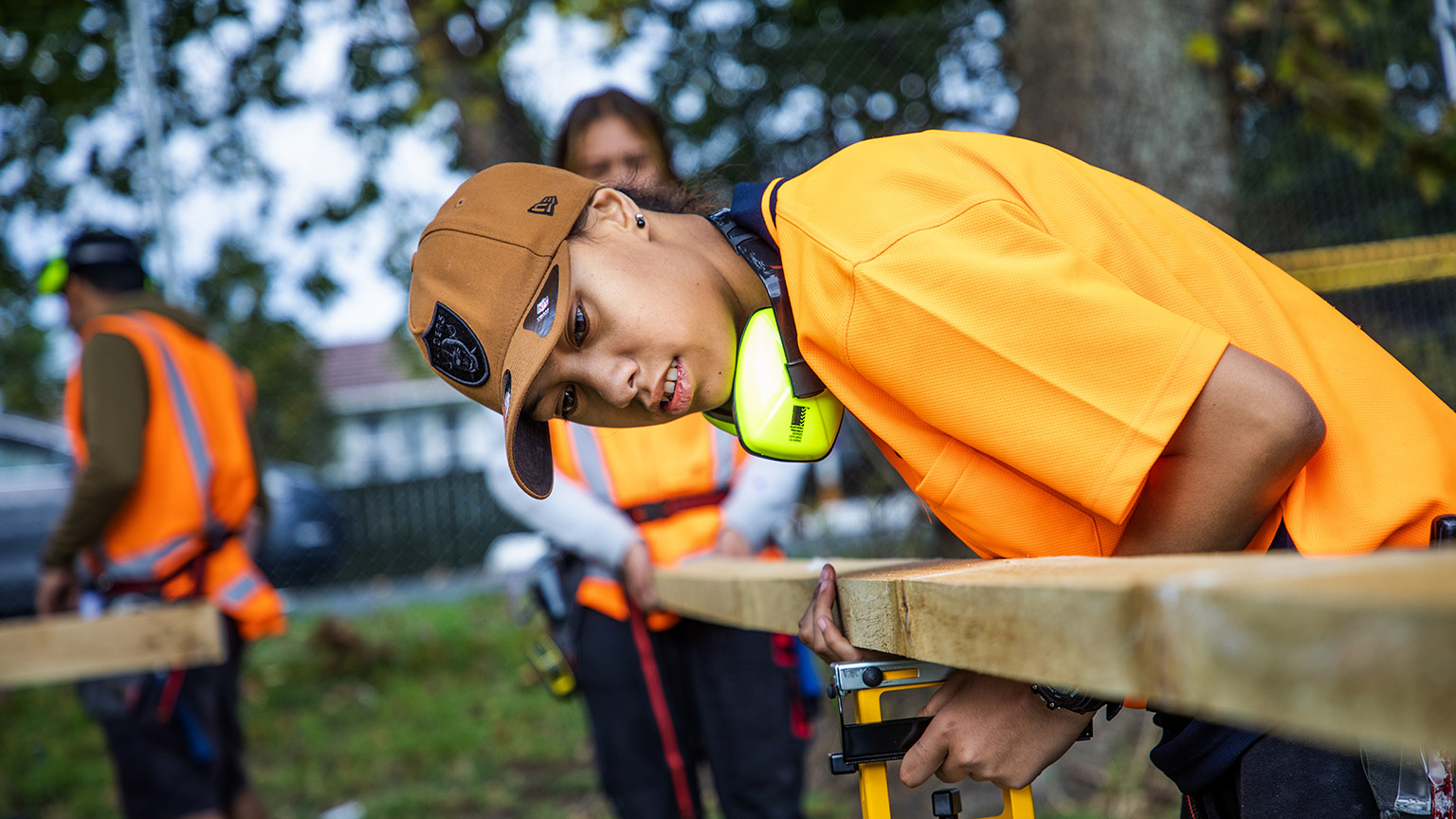