There are four concepts of building science that are related to energy efficiency. They are physical forces affecting the integrity of structures. They must always be discussed because they are primary climate- and weather-based physical mechanisms that drive the building's actions.
![]() |
![]() |
![]() |
![]() |
Heat flow | Air flow | Moisture flow | Solar radiation |
One method of improving energy efficiency is to control heat flow. This is called thermal control. If heat is reduced by good insulation, electrical energy is saved. Similarly, since refrigerator walls are well-insulated, energy is often saved. To keep their contents hot, vacuum flasks and thermal cookers also decrease heat loss. Similarly, a good thermal boundary, which includes insulation, windows, and doors, not only reduces energy waste but greatly increases an occupant’s comfort. Thermal bridges can severely compromise thermal control and comfort in some building types. They are an unintended path of heat flow, using a path of least resistance through a building envelope between the outside and inside. Thermal bridges may occur where there is an interruption in the insulation or where materials with high thermal conductivity are used.
|
Air flow can be easily controlled with good ventilation. A building would not need to rely on heating and cooling systems if natural ventilation were used. Holding windows open slightly to allow hot air to flow out would contribute to energy savings since the house will not be completely reliant on an HVAC device.
Ventilation systems become more efficient by adjusting ventilation filters.
Sealing leaks in the airwill regulate ventilation systems and prevent the build-up of humidity.
|
It is good to know the term “relative humidity” to understand moisture problems in a home (RH). Relative humidity is a measure of how much water vapour is in the air, compared to how much the air would retain at a given temperature. 100% RH means that the air can carry no more water vapour at its current temperature. The target of energy efficiency in a home should be to maintain an indoor RH for comfort and health benefits in the 40 to 60 percent range (including deterring the growth of mould). RH should be below 50 percent for optimum dust mite regulation. The solution to condensation (i.e. sweating surfaces) is to decrease the air's relative humidity (which decreases the temperature of the dew point) or to make the surfaces colder (above dew point). In air conditioning, much of the energy used is to extract moisture from the air.
|
The medium for solar radiation is solar panels. In terms of energy efficiency, most solar panels today are 11 to 15 percent efficient. This proportion is also the sum of solar energy that is being converted to usable energy. Today, scientists are actively seeking to improve the performance of photovoltaic technology to improve energy efficiency. If you have a smaller roof and limited space, the right option for you might be a more powerful solar panel. These panels can be slightly more costly because of their higher performance, but they will still meet the energy requirements you need. However, with less efficient and less costly panels to help save on your construction costs, if you have a greater amount of space, you can meet your energy needs.
|
Embodied energy is the energy used by all the processes associated with building construction, from natural resource extraction and processing to production, transport, and distribution of goods.
The cumulative embodied energy of a building is determined by a complex mixture of several processed materials.
The construction of long, robust, and adaptable buildings is the single most important factor in reducing the effect of embodied energy.
Each building is a complex mix of several processed materials, each contributing to the overall embodied energy of the building. Renovation and repair often contribute to the energy embodied in the life of a house.
Material choices and construction techniques can alter the amount of energy embodied in a building's structure dramatically, as the embodied energy content varies enormously between goods and materials. It is also a challenge to determine the embodied energy of a material, part, or an entire building.
Embodied energy content varies significantly with various forms of construction. In certain ways, if it leads to lower operating energy, a higher embodied energy level may be justified. For example, in well-built and insulated passive solar houses, large amounts of thermal mass, high in embodied energy, can greatly reduce heating and cooling needs.
Embodied energy will become increasingly important as the energy efficiency of houses and appliances increases.
If the energy efficiency of the factories manufacturing them is increased, the embodied energy levels in products will be lowered. A proven demand for materials low in embodied energy is also required.
Reviewing embodied energy
Whereas the energy used in the operation of a building can be easily calculated, it is difficult to determine the embodied energy found in the structure. Sometimes, this use of resources is concealed.
In the evaluation process, it also depends on where boundaries are drawn. For instance, whether to include:
- the resources used to move the materials and personnel to the construction site
- the building shell construction materials or all the building materials required for completion, such as bathroom and kitchen fittings, driveways, and exterior paving
- upstream energy input in the production of products (such as factory/office lighting, the energy used in the manufacture and repair of material-making machinery)
- the energy embodied by urban infrastructure (roads, drains, water, and energy supply)
Gross energy requirement (GER) is a measure of a material's true embodied energy, which preferably will contain all the above and more. This is generally impractical to measure in practice. This is generally impractical to measure in practice.
The requirement for process energy requirement (PER) is a calculation of the energy directly associated with the manufacture of the material. Measuring this is easier. Consequently, the PER is based on most of the statistics cited for embodied energy. This will include the energy used to transport the raw materials to the facility, but not the energy used to deliver the finished product to the construction site.
PER accounts for 50-80 percent of GER in general. Even within this narrower definition, it is impractical to arrive at a single figure for a material as it depends upon:
- the effectiveness of the individual production process
- the fuels used in manufacturing the materials
- the distance over which the materials are transported
- the quantity used for the recycled product
Depending on product, method, manufacturer, and implementation, each of these variables differs. Depending on how the embodied energy has been measured, they also differ.
Embodied energy estimates can differ by a factor of up to ten. Therefore, statistics cited for embodied energy are just general guidelines and should not be regarded as accurate. Remember the relative relationships and aim to use the lower embodied energy materials.
Try to use lower-embodied energy materials in large quantities, such as concrete, bricks and timber. Materials with high energy content such as stainless steel are often used in much smaller amounts.
Embodied energy per construction material
The typical figures for some Australian materials can be found below. A substance’s embodied energy becomes greater in proportion to the amount of processing needed to produce it.
Material |
PER embodied energy MJ/kg |
Kiln dried sawn softwood |
3.4 |
Kiln dried sawn hardwood |
2.0 |
Air dried sawn hardwood |
0.5 |
Hardboard |
24.2 |
Particleboard |
8.0 |
MDF (medium density fibreboard) |
11.3 |
Plywood |
10.4 |
Glue-laminated timber |
11.0 |
Laminated veneer lumber |
11.0 |
Plastics — general |
90.0 |
PVC (polyvinyl chloride) |
80.0 |
Synthetic rubber |
110.0 |
Acrylic paint |
61.5 |
Stabilised earth |
0.7 |
Imported dimensioned granite |
13.9 |
Local dimensioned granite |
5.9 |
Gypsum plaster |
2.9 |
Plasterboard |
4.4 |
Fibre cement |
4.8 |
Cement |
5.6 |
In situ concrete |
1.9 |
Precast steam-cured concrete |
2.0 |
Precast tilt-up concrete |
1.9 |
Clay bricks |
2.5 |
Concrete blocks |
1.5 |
Autoclaved aerated concrete (AAC) |
3.6 |
Glass |
12.7 |
Aluminium |
170.0 |
Copper |
100.0 |
Embodied energy of finished products
Embodied energy for assembled floors
Assembly |
PER embodied energy MJ/m2 |
Elevated timber floor |
293 |
110mm concrete slab-on-ground |
645 |
200mm precast concrete, T beam/infill |
644 |
Embodied energy for assembled roofs
Assembly |
PER embodied energy MJ/m2 |
Timber frame, concrete tile, plasterboard ceiling |
251 |
Timber frame, terracotta tile, plasterboard ceiling |
271 |
Timber frame, steel sheet, plasterboard ceiling |
330 |
Investing in energy efficiency, ventilation, and indoor air quality for heating, ventilation and air conditioning (HVAC) is a good business decision. In industrial buildings and office spaces, HVAC systems usually account for as much as 30 percent of energy usage and costs. There are many heating and cooling systems, including reverse cycle air conditioners, electrical space heaters, wood-burners, and ducted gas heating. These technologies can differ significantly in their energy efficiency, emission intensity, and indoor air quality.
As well as the effect of HVAC on overall energy usage and costs of the plant, these systems often dominate the peak demand for electricity in buildings. Improving the efficiency of a device will decrease peak demand charges. HVAC capital and repair costs also account for a large proportion of construction costs and can be reduced by good system design.
Although substantial energy and capital savings can be made by investing in modern, high-efficiency HVAC systems, it is also possible to refine existing systems. Strategies include reducing HVAC demand, fine-tuning controls and good practices for maintenance.
An integrated solution involving the following steps relies on a successful energy efficient HVAC strategy:
Decrease demand
Methods for decreasing HVAC demand include:
- improved insulation of buildings
- high-performance glazing with windows
- all-natural ventilation
- shading of exterior windows
- proper coverings for windows
Painting roofs with white paint or special reflective coatings can significantly reduce air-conditioning loads, particularly on large, flat metal buildings such as warehouses. Cooling and heating loads may also be minimised by managing internal heat generation from lighting and appliances, and minimising air leakage.
Optimise
The use of control systems and thermostats, modifications to ventilation and distribution systems, and the relocation of HVAC units may be needed for HVAC optimisation. Substantial energy savings will result from investing in better regulation, zoning and good maintenance.
Minor changes may also be made to the thermostat set points, resulting in energy savings without reducing occupant comfort.
Engineering advances allow the measurement of many factors, such as humidity, air movement and surface temperatures of nearby objects, such as windows, that influence the comfort of building occupants. Further energy savings may result from optimising these factors.
Upgrading
Distribution fan and pump energy usage may be equal to real heating and cooling generation loads in mild climates. Mechanical HVAC energy usage can be halved by several more energy-efficient HVAC systems, some of which utilise passive heat transfer or low airflow speeds. Installing such systems in milder climates, combined with strategies to minimise demand for HVAC services, will lead to substantial electricity savings.
As HVAC systems are responsible for up to 30 percent of water usage in commercial buildings, this can also produce significant water and commercial waste savings. An emphasis on updating and correct sizing of the heating and cooling units will significantly boost performance in more extreme climates. The best available reverse cycle air conditioners are around 30 to 40 percent more powerful than the 'minimum norm' versions that are currently available.
Innovation
At several stages, advances in HVAC systems are occurring. To offer energy savings, ventilation, and indoor air quality of about 17 percent, several component technologies are bundled into advanced rooftop air conditioners. During later uses, thermal energy storage systems store heat or cold for use, preventing part-load operation and moving peak loads to off-peak hours.
Active solar thermal systems, a modern form of heating and cooling system, use free solar radiation to minimise peak demand, which is available for a significant portion of the year in Australia. Software technologies are improving the management and efficiency of HVAC systems and building integration more and more. With enhanced air-handling management techniques, increased use of economic cycles, night-time passive ventilation, and heat recovery are all feasible.
With the ever-evolving technology, it is advisable to regularly research for innovative heating, ventilation and air conditioning systems, using the internet or trusted sources to find the most appropriate solution for the building and construction project.
Moisture barriers
Moisture can cause severe damage to your home and pose serious health risks. By using moisture barriers, you can make one simple enhancement that can not only protect its structure, but also protect your family's health and at the same time save you money. Installing a moisture barrier in the crawl space under your home will remove moisture and provide you with not only these advantages, but also others.
Here are seven advantages of the construction of moisture barriers:
- Regulation of temperature
- Prevention of mould
- Safegaurding the pipes
- Electrical risk
- Integrity of structure
- Regulation of pests
- Energy efficiency
Regulation of temperature
The temperature inside your home can be influenced by moisture in your crawl space, making it more difficult to maintain a constant temperature during the day. As it fails to control temperatures, this puts extra pressure on your HVAC system. This moisture is removed by installing a moisture barrier in your crawlspace, allowing your HVAC system to better maintain a constant temperature during the day.
Prevention of mould
The ideal environment for mould and mildew development is increased humidity in your crawlspace. This mould can cause severe health issues for your family and can cause your home to suffer major harm. You can reduce the moisture in your crawlspace by adding a moisture barrier, helping to stop the formation of mould and mildew.
Safeguarding the pipes
Water and utility pipes also run in your crawlspace. As humidity levels rise, these pipes can burst and break. The addition of the moisture barrier prevents this excess moisture, helping to protect your pipes and protect your finances from expensive repairs.
Electrical risk
Many of the utility pipes in your home, including those that house electrical wires, run through your crawlspace. They can grow shorts, rust, and even catch on fire when these wires are exposed to moisture. Through a moisture barrier, minimising the moisture in your crawl space helps shield these wires and your home from the risks of electricity.
Integrity of structure
Many of your house's structural elements are made of wood. Moisture in your crawlspace on these components may contribute to wood rot. Damage to these systems and excessive repair bills can cause severe damage. You slow down wood rot and protect the structural integrity of your home by reducing the humidity in your crawlspace with a moisture barrier.
Regulation of pests
The perfect shelter and an ample supply of water for pests and wildlife is offered by your crawlspace. You remove this point of entry for rodents and other animals into your home by sealing the crawlspace completely with a moisture barrier.
Energy efficiency
Your HVAC system uses more power as it runs longer to regulate temperatures in your house, which causes your energy bills to rise. This additional work also brings more wear and tear on your HVAC machine, leading to more expensive repairs and replacements. The installation of a moisture barrier seals the crawlspace, controls the levels of moisture, and reduces the pressure on your HVAC system. This contributes to more energy savings and lower bills for utilities.
Vapour barriers
A vapour barrier (sometimes referred to as a vapour retarder) is usually a sheet of plastic or foil used for damp testing in various building assemblies, such as walls, roofs, foundations, and floors, to prevent condensation from developing. Vapour barriers or vapour diffusion retarders can boost energy efficiency and comfort in a typical commercial building or home, while also avoiding moisture and dampness issues.
The goal of the vapour barriers
In building design, the vapour barrier is an essential part. The goal is to help prevent water vapour from reaching building walls, floors, attics, crawl spaces or roofs, where it can condense and cause mould to rot or develop building materials.
Water condensation damage due to the movement of water vapour (called 'water vapour drive') will wreak havoc on even the most durable of constructed structures and threaten the effectiveness of insulation. By learning when, how, why, and where to incorporate a vapour barrier in your next project, you can save yourself this expensive headache.
What is vapour in water?
Water vapour is water in its gaseous state (instead of as a liquid or solid), and it is completely invisible. Water vapour continuously diffuses from the wet, humid interior of a house to the cold, dry exterior through construction materials. When water vapour passes through a wall, roof or other barrier and reaches a surface with a temperature below the dew point (when water vapour condenses), it becomes condensation and a hazard to the construction materials' integrity.
Water vapour transmission is an important but very confusing issue, according to sustainability expert and architect Daniel Overbey. The driving force behind vapour transmission is the difference in vapour pressure between the two sides of a building envelope assembly.
Many daily human activities, such as laundry, cooking and bathing, release water vapour into a building and raise its humidity. Via diffusion, this air then naturally tries to find a way out of walls, ceilings, etc. For commercial buildings, the same is true, although the activities that take place inside can be different.
Construction in a cold climate
Some might ask, is a barrier to vapour necessary? Your first move, as a builder, is to consult your local and provincial/state construction codes. Vapour barriers are a necessary part of building construction in many climates.
In warmer climates, you will find that vapour barriers are often not needed. Also, a vapour barrier can do more damage than good if built in the wrong environment or on the wrong side of building materials. This situation can prevent the drying of water vapour, which in turn can cause rot and mould.
You may need to check with other contractors in your area or calculate the needs of your building according to standards set by proven professional organisations if you are unsure about the building specifications. For instance, in any environment where the outside average temperature is below 4° C degrees and the predicted internal winter relative humidity is 45 percent or greater, it is recommended to have vapour barriers on the interior side of a roof.
What is a vapour barrier going to do?
To prevent moisture from spreading and potentially causing water damage, vapour barriers are built along, in or around walls, ceilings and floors.
A true vapour barrier, as calculated by the ‘moisture vapour transmission rate’, is one that fully prevents moisture from moving through its content. If even a small amount of permeability is in the material, but the barrier still provides moisture protection, this is called a vapour diffusion retarder.
Vapour retarders are often usually referred to simply as barriers to vapour. The barrier terminology is less precise since the vapour is not completely barricaded by the goods in most situations.
What am I authorised to use as a vapour barrier?
- To build effective vapour barriers, a large range of materials are available, including:
- coatings that are elastomeric
- foil with aluminium
- aluminium with paper-backing
- plastic sheet of polyethylene
- kraft paper with asphalt-coating
- metallised film
- vapour retarder paint
- extruded polystyrene or foil-faced foam surface
- exterior-grade plywood
- sheet-type membranes for roofing
- glass and metal
Materials are graded by their permeability in the International Residential Code (IRC). A unit called a "perm" is used when calculating this. For a material has a perm rating of 1.0, when the vapour pressure difference between the cold side and the warm side of the material is equal to 1 inch of mercury (1 inch Hg), 1 grain of water vapour will pass through 1 square foot of the material in 1 hour. One grain of water is equal to 0.064799 grams.
The materials for vapour retarder are divided into one of three types:
Class I vapour retarders (0.1 perms or less):
- metal sheeting
- the layer of polyethylene
- membrane rubber
Class II vapour retarders (greater than 0.1 perms and less than or equal to 1.0 perms):
- unfaced polystyrene that is expanded or extruded
- thirty-pound asphalt paper with coatings
- kraft paper coated with bitumen
Class III vapour retarders (more than 1.0 perms and less than or equivalent to 10 perms):
- gypsum board
- insulation of fiberglass (unfaced)
- insulation of cellulose
- board lumber
- block concrete
- fifteen-pound coated paper on asphalt
- house wrap
Experts agree that most issues with condensation arise due to air leakage, not vapour diffusion, so make sure you use an air barrier to properly seal penetrations (such as flashings) for air leakage.
How air barriers vary from vapour barriers
Some equate a vapour barrier to a raincoat, whereas a windbreaker appears more like an air barrier. You may not need a vapour barrier in certain situations, but you may need an air barrier to prevent water vapour from migrating through air currents instead. This is the number one way to drive water vapour into homes and assemblies (such as walls or roofs). In fact, air flowing through holes and cracks is 30 times more likely through building assemblies to carry water vapour than through simple water vapour diffusion.
A vapour barrier, on the other hand, helps avoid the second most common method of movement of water vapour: vapour diffusion. This is ‘the slow movement’ from regions of higher to lower water vapour concentration (higher to lower vapour pressure) of individual water vapour molecules. Condensation is caused by cooling hot air as it passes through building materials such as insulation and drywall.
A vapour barrier is not meant to prevent the passage or migration of air; that is the role of an air barrier. So, while a vapour barrier must be continuous, a vapour barrier does not need to be as tightly sealed, unlike an air barrier.
Some products, such as the AquaBarrier, serve as both a vapour and an air barrier. In hot, southern climates where moist exterior air is commonly found, these are also used. In any location where both the air barrier and the vapour barrier are situated on the warm side of the building assembly, combined vapour/air barriers are also suitable.
Vapour barriers for industrial roofs
In flat roof construction, vapour retarders are commonly used to stop moist air from the inside of the building condensing into the roof assembly and possibly causing material harm. These products are an effective way of maintaining the thermal quality of roof insulation and are therefore an integral part of protecting a home or commercial building's comfort and energy efficiency. In most cases, it should have a perm level of 0.5 or less when mounting a vapour retarder on a roof deck.
The vapour barrier must also be warm enough to remain above the dew point on the outside side to function effectively, which ensures that ample insulation must be built over the barrier to preserve the temperature, regardless of the weather outside.
With the ever-evolving technology, it is advisable to regularly research for innovative solutions for improved moisture and vapour barriers, using the internet or trusted sources to find the most appropriate solution for the building and construction project.
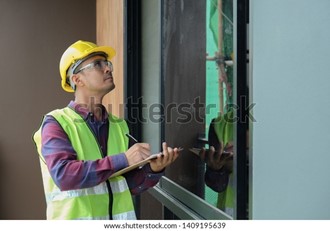