Contract documentation
Contract documents are written documents that specify the duties, obligations, and work of the construction contract and are legally binding on the parties to the contract (owner and contractor).
It is necessary for the person drafting the contracting specifications and other documents to clearly understand what the effects of the contract documentation do and do not constitute; failure to properly classify the contract documents may be a major contractual flaw.
Following the contract-writing axiom ‘say it once in the right place’, what constitutes the contract documents should be indicated at only one venue (preferably the owner-contractor agreement). The listing of the contract documentation should be complete and unambiguous to maximise the potential for consistent interpretation and should not include any documents that should not rightfully constitute contract documents.
In this respect, common examples of vagueness include phrases such as ‘the contract documents... include all exhibits, attachments, supplements, and all other such documents used as contract modifications’ and the common practice of including appendices in the project manual but omitting those appendices from the list of the contract documents. It is worth avoiding such vagueness.
These are several parts of contract documentation:
Part of Contract Documentation | Definition |
---|---|
Contract documents | Documents that are designated in the agreement and altogether comprise the contract. |
Bidding documents | These are the proposed contract documents and all bidding requirements. |
Bidding requirements | These are the advertising or invitation to bid, instructions to bidders, bid bond or other bid protection, if any, the bid type, and the bid with any attachments. |
Drawings | This is the section of the contract that describes the complexity, scope, and purpose of the work to be done by the contractor. |
Specifications | This is the portion of the contract consisting of written content, equipment, processes, specifications, and workmanship criteria as applied to the work and certain administrative and procedural requirements relevant to the work. |
Shop sketches | All drawings, diagrams, illustrations, schedules, and other documents or information explicitly planned or assembled by or for the contractor and submitted to illustrate any portion of the work by the contractor. Whether accepted or not, shop drawings are not drawings and are not contract documents. |
Project manual | This is the written document prepared for the procurement and design of the work, including but not limited to bidding documents or other construction procurement documents, information on geotechnical and current conditions, the agreement, bond forms, general conditions, additional conditions, and requirements. In one or more volumes, the contents of the project manual can be bound. |
To summarise, be aware of and correctly draft the clauses on what the contract documentation constitutes.
Unusual aspects of construction
Even if you use a standard type of contract, various types of construction that are out of the ordinary can be included in this contract.
This may not be protected in the contract's wording, but you can see this distinct type of construction by looking at the plans and specifications.
The inclusion of a portion of raked ceiling inside the house can be an example of this. This is a very simple difference but planning the design of this house will make a great difference.
There are restrictions that are imposed on the forms of construction when constructing in some regions. There will be several different aspects of construction, including the use of materials and style of construction that would not be used in other fields, for example, if the building is in a bushfire-prone area.
It is also important to ensure that you look carefully at all the documents contained in the agreement.
Ensure that you carefully read the plans along with the requirements so that every distinct aspect of construction can be decided. These are often explicitly noted in the contract, and it is also important to read the agreement carefully as well.
The contract may have been drafted by others in the company. If this is the case, during the preparation of the construction project, it will be important to consult them.
Use of materials
The contract documentation may place limits on the use of certain materials or on the other hand, may specify that certain materials must be used. At times, the plans and/or specifications may note these materials and how they are to be used. This may be noted within the contract itself.
Before starting the construction of the project, it is necessary to ascertain in the contract documentation what materials are to be used and how they are to be used. This then needs to be included in the planning of the project.
Penalties
When you are negotiating dates for the work to be completed, be careful on how the other party might charge for liquidated damages. Liquidated damages are the compensation that you might have to pay if you do not complete construction on time.
Liquidated damages usually represent pre-estimates of the loss they will likely incur if you do not complete the work on time. They are not meant to penalise you for finishing work late.
For example, you entered into a construction contract to build a house but did not complete the construction on time. Therefore, the rate of liquidated damages should reflect the other party’s costs of being forced to delay the moving in to the house. These costs might include the amount of rent they may have paid if there was no delay.
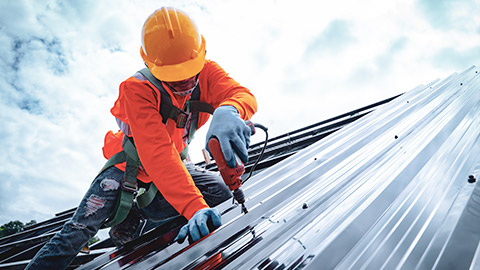
In the past, builders only used subcontractors to perform 'specialised' tasks. They completed most projects with their own labour. Today, the commercial builder subcontracts much of their work, acting primarily as the supervisor.
Subcontractors are used on construction projects as they:
- Provide specialised labour for particular construction tasks
- Provide skilled tradespeople who can undertake specialist work, and achieve an acceptable standard
- Lower cost of work
- Reduce builder's overhead costs, such as those associated with workers’ compensation and other direct employee benefits
- Reduce overall builders risk.
Subcontractor management
Good subcontract management is important in today's legal climate. Because many risks have been shifted from the head contractor to the subcontractor, the nature of contracts between builders and subcontractors has increased in importance. Informal agreements and understandings generally have been replaced by contractual agreements. Subcontracts have legally binding provisions for both parties. Fulfilment of the obligations of the subcontract agreement is necessary for completion of the construction project. Subcontractors can affect the project's profitability through delays, poor workmanship, or default of contract. The quality of subcontractor management is linked to the profitability of the project.
Buy out
The process of converting all subcontractor tenders to subcontracts and all quotes to purchase orders, or purchase contracts, is often called "buy out." This is best accomplished at the beginning of each new job, and can affect the project's running and profitability.
In the process of selecting a subcontractor, the builder needs a system to compare quotes meaningfully. This is known as scope alignment or tender analysis. The person assessing each subcontractor’s quote must identify and understand any qualifications, inclusions, and exclusions given. The process may require the builder asking the subcontractor to clarify aspects of their quote. A letter of intent indicating that a subcontract will be signed shows good faith and will get things moving for the subcontractor. The final steps of the "buy out" are to complete a final subcontract agreement that is signed by both parties.
Be aware that exclusions included in the subcontractor's quote may be a way of transferring risk to the head contractor. Note that if the owner has accepted an alternative to the proposed scope of works, it needs to be reflected in the price. These are important provisions, and one should understand the consequences of changes in these clauses. It should be noted that many builders are now adding additional "General Conditions" to their subcontracts.
Subcontractor requirements
Subcontractor requirements for a project can be determined by:
- identifying, matching and verifying subcontract skills sets with project work requirements
- identifying work sequence and nature of job roles
- calculating number of hours required to perform the work
- calculating number of subcontractors required by the hours within the timeframe
- determining total hours required for each function and stage of work
- estimating project timeframe from start to finish.
The builder's on-site personnel should have a good understanding of the subcontracting process.
On-site personnel should understand the following:
- The nature of the subcontractor's business
- The scheduling demands on the subcontractor
- The risks the subcontractor is facing on the project
- The equipment and safety concerns of the subcontractor.
Subcontractors vary from very small firms to large international firms. Subcontractors specialise in a certain construction works, such as floor covering or mechanical or electrical work. Many subcontractors are involved in a number of concurrent projects, which can be challenging with finite resources. A building subcontractor may undertake works in the residential, commercial, industrial, or heavy construction sectors of the industry.
Construction quality
Claims against defective building work are a growing trend. The purpose of a construction quality control program is to prevent claims by ensuring good workmanship, the use of materials fit for purpose, and proper documentation. The use of sub-contractors that do not have effective quality assurance programs increases the potential for claims for defective building work.
To prevent the possibility of claims against defective building work, contractor selection efforts should:
- have a QMS (Quality Management System) policy in place that emphasises quality workmanship.
- develop and implement quality and safety controls for the construction process.
- assign responsibilities for quality to all employees and sub-contractors
- use the materials specified. If you believe that the incorrect material has been specified, it should be brought to the attention of the Superintendent (e.g the architect).
- verify that materials received meet the specifications selected.
- ensure tradesmen have adequate skills or expertise.
- ensure proper installation of materials components.
- have an inspection process in place that identifies and corrects improper materials or installations prior to accepting the phase of the job.
- implement a completed project checklist to verify that all job requirements have been met.
- receive acceptance sign-off from the owner or general contractor.
- retain job records for future reference and use.
Contractors’ liability issues continue to emerge and challenge the profitability and insurability of contractors. However, contractors can reduce their exposure to risks. Seeking legal and insurance advice can be useful.
Subcontractor selection
Head contractors want subcontractors to complete good quality work at a fair price.
The subcontractor selected will be acting on behalf of the builder to complete the contracted job. While the use of sub-contractors can help bring additional expertise and resources to the job and help control project costs, it can also increase exposure to liability, workers’ compensation, and even automobile liability claims.
Exposure to subcontracted related claims can result from the use of uninsured subcontractors, third party over actions and defective workmanship.
It is recommended you discuss the risks associated with subcontracting with your insurer before developing a policy that suits your needs.
Subcontractor selection criteria
The following factors would be useful in selecting subcontractors for residential construction.
- Price: should not be the only factor that determines whether a subcontractor is selected. Experience, reliability and the quality of past work should also be taken into account.
- Good management practices: Subcontractors should have good management practices, including meticulous work schedules.
- Flexibility: Subcontractors need to manage and organise their resources at all times, allowing themselves to be flexible.
- Good working relationships: Subcontractors who cultivate good working relationships between their workers as well as other subcontractors and the head contractor can help a job run smoothly.
Uninsured subcontractors
It is important to verify that any subcontractor completing work on behalf of the head contractor has appropriate and current insurances.
Subcontractors should have current:
- Workers’ Compensation insurance
- Public liability person and property insurance covering injury to third parties and their property
- Automobile Liability appropriate to the work they are undertaking
- Where appropriate, a contractor's all risk policy covering the works and damage resulting from the works
- On rare occasions, product liability insurance
- Professional indemnity insurance where design is involved or appropriate.
Subcontractors with active and effective safety programs should be selected.
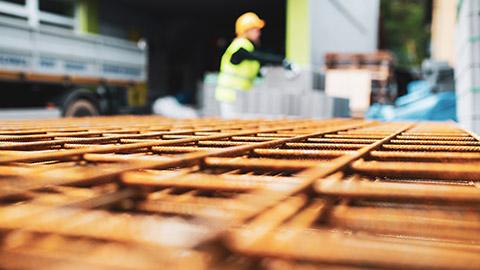
Supplier evaluation and improvement processes are the most significant variables in the effective management of construction management, as they improve organizations through the channels of high-quality products and customer satisfaction.
The traditional approach has been to rank and select suppliers solely on the basis of price. However, moving from ranking/selection to selection/improvement decisions in the contemporary supply-chain network is complicated, as potential options for selection/improvement decisions are evaluated using multiple criteria. Therefore, supplier selection/improvement has become a problem that includes several tangible and intangible factors.
Recently, these criteria have become increasingly complex, interdependent, and dynamic as environmental, social, political, and customer satisfaction concerns have been added to the traditional factors of quality, delivery, cost, and service.
When assessing material suppliers for building and construction, we need to make sure all compliances are covered. With any building and construction material, the requirement for compliance to Australian Standards and the National Construction Code must be confirmed before purchasing.
Liaise with suppliers
You probably have determined what suppliers you will use for the materials necessary for the project at the time of calculating the project price. By liaising with suppliers, you can ensure that the supplies for the project are available.
Remember the following things:
- Suppliers: It is important to appoint what suppliers you are going to use to supply these products before planning material schedules.
- Lead time: You will need to integrate this lead time into the plan if you are using a software application.
- Call forward sheets: You will need to prepare call forward sheets to allow you to have the materials ordered at the correct time.
- Arriving on-site: It is crucial to have your materials arrive on site. This helps the planned work to proceed.
Identify alternative suppliers
If a supplier is unable to procure the materials needed between the tendering period for the project and the signing of the contract for the project, it is important to find an alternate supplier.
You will usually have found alternative suppliers during the estimation and tendering process. If your first supplier option was not able to meet the specifications, you may go to these other suppliers. With these new vendors, you will need to ensure that they can deliver the materials at the time required for the project.
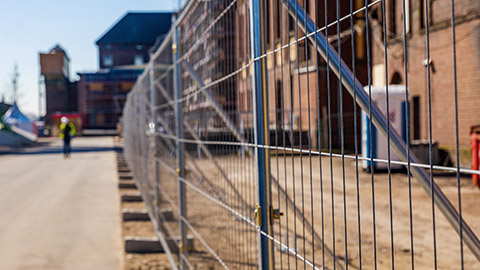
Before accessing the site undertaking due diligence for access and site limitations must take place. Imagine organising all the trades and materials to start with no parking or material storage locations.
Access and egress mean the entry or exit to an urban object, such as a building. Access and egress are a specific form of the general concept of accessibility. It includes footpaths, corridors, doorways, gates, steps etc., which may provide a means of access and egress, to be suitably constructed, kept free from obstruction and to be well maintained. The BCA (NCC) outlines the minimum requirements for access and egress in accordance with buildings and building sites.
Access
- Determine site access for entry and exit of delivery trucks. Ensure there is adequate room for trucks to stop and use lifting equipment such as forklifts from the side of the road onto the site.
- Check access for cranes on-site, taking into account their height and length and requirements for setting up space.
- Check if excavation works need to be undertaken to enable access for machinery. If this is the case, barriers may be required for additional protection of footpaths against water, mud and soil.
Traffic
- Check if traffic control is required, especially if large pieces of equipment such as cranes are required.
- Check there is adequate control over vehicles entering and leaving the site. Is there enough room to allow for their turning circles?
- Check provision of parking for workers adjacent to the site, in on-site parking or via parking controls in the street (this is often a problem with neighbours).
Entrance
- Inspect existing kerbs and record any damage along the full length of the frontage.
- Inspect the nature strip and record any damage along the full length of the frontage.
- Check if protection is required for existing nature strip, crossover and footpath.
Site overview
- Take levels of the site at each corner and at various measured distances along all boundaries.
- Prepare a contour plan of the site with reference to a relevant datum point or if available, Australian height datum (AHD).
- Locate all trees, major shrubs and plants and plot and sketch their location on a plan or take photos.
- Inspecting adjacent properties to ensure the construction work is not going to cause any damage. You will learn more about inspecting adjacent properties in Subtopic 6.1 Inspecting adjacent properties.
Boundaries
- Locate boundary pegs at all legal corners of the site using 50 x 50 mm white pegs (in new sub-divisions, these pegs often have identification stamps or plates).
- If the above pegs cannot be located, ask the owner to provide your company with a re-establishment survey (re-peg) which will re-establish the legal boundaries of the site. It is in your interests to ask for the re-establishment survey up front.
Note: Do not take the location of fences or structures built on the boundary line as being the legal line of a boundary! There may be a significant difference between the legal boundary and the actual fence line or structures.
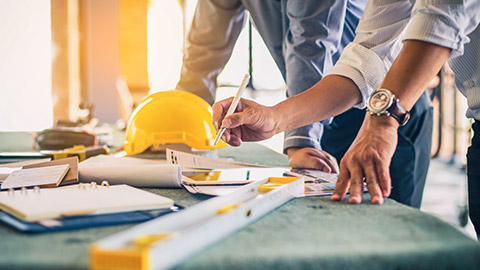
A project schedule is a plan of all the tasks and activities that need to be completed on your building project. It shows the order in which these are to be done and provides a timescale for the completion of each activity. A project schedule is a living document that you will need to track and revise throughout your project to ensure the project is completed on time.
When you prepare a project schedule, you will plan the sourcing and ordering of materials, sequence of trades, produce labour and materials schedule, produce a cashflow chart and regularly revise and update the schedule.
Scheduling will be helpful in planning the following:
- Start and finish dates
- Delivery of materials on-site
- Provision of labour on-site.
It also helps in producing a critical path form of events and analysing the project performance. It is important to pay attention to the tasks on the critical path. If tasks are falling behind schedule, especially critical tasks, action needs to be taken to ensure that the entire project does not end up running over schedule.
At the end of the module, at the Additional Resources, you can access a project schedule template.
Commencement date
You will be able to set the start date of your project after you have met with regulatory authorities or private certifiers. The regulatory authorities of construction are the building surveyors. The Australian Institute of Building Surveyors manages the building surveyors in the country.
Nationally and globally, the Australian Institute of Building Surveyors is regarded as the top professional body representing Australia's building survey practitioners.
A building surveyor is a specialist who is charged with understanding the method of construction control. A building surveyor has the power to review construction plans to ensure that they comply with the Building Code of Australia, the Australian standards referred to therein, and any other applicable building acts or other laws or regulations of the jurisdiction in which the building is built. Building surveyors are either municipal or private. It is the duty of building surveyors to ensure that buildings are safe, usable, and energy-efficient. They have an impact on a building’s design, planning, and functionality.
Codes, standards, and regulations
The permits needed for projects can vary depending on project form, location, and project size. To obtain the requisite approvals, you must efficiently recognise and communicate information with the relevant regulatory authorities.
However, before construction can commence, all permits must be issued. It is also important to ensure that all relevant approvals are included in the planning stage.
You would need to decide what approvals need to be obtained in this planning process, as well as what links need to be made to the building or construction site. If these are included in the planning phase, you can then continue to receive these permits and arrange the appropriate service connections, such as electricity, water, telephone/broadband, sewerage and gas.
Depending on your state/territory's construction regulations, you also need to factor in regular inspections completed at the different stages of the building and construction process. Generally, you would need to consider the following building stage inspections:
- Footing inspection
- Slab inspection
- Frame inspectionLock-up inspection
- Fixing stage inspection
- Handover inspection/ Practical completion.
You can read more about these types of inspections from House Inspect Australia's website, a company specialised on building inspections. Note, that building inspections may vary by state/territory building regulations, so always make sure you consult your local regulator.
Copies of plans, sketches, and standards
Plans, drawings, and specifications included in the documents of the contract must be sent to the regulatory authorities for the approvals required. Depending on the type of project, the types of approvals required would differ.
You will need to contact the local regulatory authority to see what applications you need to apply for your building or construction project. Another approach is to hire a private certifier who will advise you on what applications for the project need to be submitted.
Once you have been notified of the applications that need to be submitted, you can provide to the regulatory authority or private certifier the plans, drawings, and requirements for this document.
Environmental applications
Under the Environment Protection and Biodiversity Conservation Act 1999, some projects require environmental applications to be submitted for approval to the Environmental Planning Authority (EPA). Until this permission has been given, work must not begin on the project.
The eight matters of national environmental significance protected by the EPBC Act are:
- world heritage properties
- national heritage places
- wetlands of international importance (listed under the Ramsar Convention)
- migratory species protected under international agreements
- listed threatened species and ecological communities
- Commonwealth marine areas
- the Great Barrier Reef Marine Park, and
- nuclear actions (including uranium mines).1
The EPBC Act provides a legal framework to protect and manage nationally and internationally important flora, fauna, ecological communities and heritage places defined in the Act as matters of national environmental significance. The Environment Protection Authority (EPA) regulates to prevent pollution and waste in the environment. There is no single EPA that regulates Australia as a whole. There are various EPAs in different states.
It is prudent to seek guidance from experts about the need for them and their timing when it comes to environmental applications.
At the end of this module, at the Additional Resources, you can access a document published in 2019 by EPA that provides guidance on how to develop a construction environmental management plan. The Additional Resource folder contains a draft environmental management plan, an EPA development checklist with information required when referring a development application to EPA and a completed sample environmental report for your reference. These documents will give you a better insight to the environmental requirements and related documentation.
There is a variety of environmental legislation in Australia. You can find a list of legislation on the Department of the Agriculture, Water and the Environment’s website. Environment-related regulations vary from state to state, so always make sure you are aware of the relevant state/territory regulation.
For example:
State/Territory | Examples of environmental regulation |
---|---|
ACT |
Environment Protection Act 1997 Environment Protection Regulation 2005 Magistrates Court (Environment Protection Infringement Notices) Regulation 2005 Water Resources Act 2007 |
NSW |
Contaminated Land Management Regulation 2013 Environmentally Hazardous Chemicals Regulation 2017 Protection of the Environment Operations (Clean Air) Regulation 2010 Protection of the Environment Operations (General) Regulation 2009 Protection of the Environment Operations (Waste) Regulation 2014 (Waste Regulation) |
QLD |
Environmental Protection Regulation 2019 Environmental Protection (Air) Policy 2019 Environmental Protection (Noise) Policy 2019 Environmental Protection (Water and Wetland Biodiversity) Policy 2019 |
VIC |
National Environment Protection Council (Victoria) Act 1995 Pollution of Waters by Oils and Noxious Substances Act 1986 Environment Protection (Distribution of Landfill Levy) Regulations 2010 Environment Protection (Fees) Regulations 2012 Environment Protection (Industrial Waste Resource) Regulations 2009 Environment Protection (Scheduled Premises) Regulations 2017 Environment Protection (Residential Noise) Regulations 2018 Environment Protection (Vehicle Emissions) Regulations 2013 |
NT |
Waste Management and Pollution Control Act 1998 Environment Protection (Beverage Containers and Plastic Bags) Act 2011 Northern Territory Environment Protection Authority Act 2012 Waste Management and Pollution Control Act 1998 |
TAS |
The Litter Act 2007 National Environmental Protection Council (Tasmania) Act Plastic Shopping Bags Ban Act 2013 Marine-related Incidents (MARPOL Implementation) Act Land Use Planning and Approvals Act 1993 |
You can use the Protected Matters Search Tool to help understand if your proposed site is home to, or located near, any matters of national environmental significance are likely on, or near, your proposed site.
Having climate change becoming more and more a burning issue of the past decades, there is a strong desire in the building and construction industry to build sustainable and energy efficient buildings across Australia.
Green Building Council Australia (GBCA) was established in 2002 and they aim to lead the sustainable transformation of the built environment. GBCA rates the sustainability of buildings, fitouts and communities through Australia’s largest national, voluntary, holistic rating system, the Green Star. They also educate industry, government practitioners and decision-makers, and promote green building programs, technologies, design practices and operations.
GBCA’s policy priorities are:
- carbon positive buildings
- strong government leadership
- realising our vision for cities and communities
- smarter infrastructure investments
- affordable, sustainable housing.2
Applications to parking restriction
Applications for parking limits are usually applicable to inner-city sites. You must, however, be careful of any parking limitations that apply to the vicinity around the project site. You can verify with the local council authority if there are parking limits for the area and if it is possible to apply for workers' vehicles to have access to parking in those areas.
At the end of the module, at the Additional Resources, you can view an example Traffic Management Plan (TMP), a completed sample traffic management plan and a general guide published by Safe Work Australia on traffic management.
Regulatory approval procedures and timeframes
You need to be familiar with the procedures and timeframes required for regulatory approvals during the planning phase. These must be considered in order for you to schedule a time for the start of work.
Planning permits give permission to develop or use land in a particular way. You may require a planning permit for a new home, extension, renovation or an additional dwelling on the land.
The local council is responsible for issuing a planning permit. If you need a planning permit, it must be issued from your local council before you can obtain a building permit. Planning permit applications submitted to council may need to include the proposed design, planning report, shadow diagrams and other relevant documentation. Contact your local council for more information.
Applications for building permits
A formal application for a building permit is made when you are ready to start construction. The application must be signed by each owner, so that they consent to the work being done on their land, and by the builder who will be responsible for the work. The application must also include details about the proposed building or incidental structure, evidence that prescribed approvals have been complied with, and must be accompanied by payment of the Building Services Levy and the building permit fee paid to the permit authority.
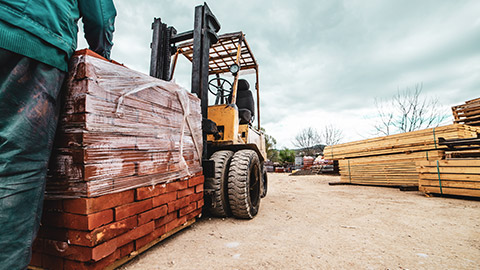
Materials and supplies being delivered to site need to be paid for as soon as possible. Often the materials are delivered by companies that have accounts with the builder.
There are a number of pieces of paper that are involved with any delivery of materials or labour work supplied to a building site. Each of these papers is interrelated.
- Order form or Purchase Order docket: this is produced by the builder prior to delivery to site.
- Delivery docket: this arrives with the delivery and is signed for by the site manager or similar. This should be cross checked against the Purchase Order or Order form.
- Invoice: this arrives at the company office from the building site or relates directly to a delivery to the building site. This should be cross checked with the delivery docket ensuring that everything charged for has been signed off as delivered.
It is important that deliveries are brought onto the site just in time, neither too early nor too late. Always provide a delivery date when an order is placed. You should generally allow three days from the date of call-up to the date of delivery.
Usually, site deliveries are controlled and recorded using a delivery sheet and diary entries. Small builders generally do not have set delivery procedures as the builder is frequently not on-site when deliveries are made. However, it is important to physically check each delivery against the delivery sheet at the earliest possible opportunity.
Every item on the delivery sheet should be located and ticked off on the sheet. If your subcontractors are reliable, they may notify the builder when a delivery arrives. If the builder is not able to be present for the delivery, the delivery sheet can be collected next time the builder is on-site. Usually, the delivery sheet is left in a sealed envelope with the goods.
If some items are missing from the delivery, you need to phone the supplier. A subsequent delivery is then organised. Sometimes a company representative will be sent with the missing supplies. Occasionally, another order needs to be sent, quoting the same order number with an 'S' added to indicate that a delivery has been 'short' in the goods received, e.g. order number 11608.
The process is similar for larger builders but often they have a delivery acceptance slip to be filled in by the site supervisor which is then forwarded to the site office.
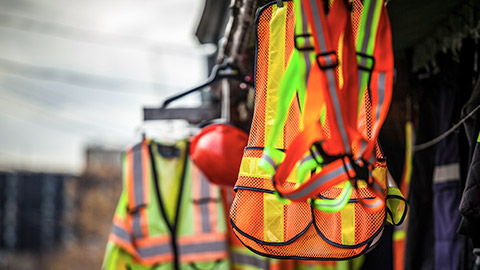
The Australian Work Health and Safety Strategy 2012–2022 has identified the construction industry as a priority due to the high number and rate of work-related fatalities and serious injuries. An industry profile compiled by Safe Work Australia in 2015 found the most common work-related injuries experienced by workers in the construction industry were:
- cuts and open wounds (31%)
- sprains and strains (21%)
- chronic joint or muscle conditions (16%).
These injuries were mainly due to:
- hitting or being hit by an object (31%)
- lifting, pushing or pulling objects (30%)
- falls from a height (15%).
When it comes to work-related fatalities, the most recent statistics from the Construction Industry Profile show that between 2003–13, 401 workers died on construction sites in Australia.3
The Harmonisation Model Work Health and Safety (WHS) laws commenced on 1 January 2012 in many states and territories to harmonise occupational health and safety (OH&S) laws across Australia with the exception of WA (OSH) and Victoria (OHS). WHS legislation includes a model WHS Act, regulations, Codes of Practice and a national compliance and enforcement policy. The model WHS Act is not significantly different from current occupational health & safety (OH&S) laws, but will make it easier for businesses and workers to comply with their requirements across different states and territories. Each state and territory is responsible for regulating and enforcing WHS laws. Safe Work Australia is the national body in charge of developing work health and safety and workers' compensation policy. Visit Safe Work Australia to read about the work health and safety laws. Work Safe is the state regulatory authority in Western Australia and Victoria.
Roles and responsibilities
Everyone has a role in the health and safety of workers and others in the workplace.
This includes:
- ‘Persons conducting a business or undertaking’ (PCBU) such as an employer
- Officers, such as owners or operators of a small business, individuals who make significant decisions in a business, or those who can affect a business’s financial standing, and
- Workers and others in the workplace.
Employer - Person Conducting Business Undertaking (PCBU)
One of the employer’s primary duties under the Act is to provide: 'such information, instruction, and training to, and supervision of, the employees as is necessary to enable them to perform their work in such a manner that they are not exposed to hazards.'
Employers owe this same duty of care to independent contractors and the contractor’s employees working at the workplace. Employers, so far as is reasonably practicable, are also responsible for the safety and health of people who are not employees. Employers need to take all practicable steps to ensure that the work of the employer or employees does not harm any other person while at work, including members of the public or visitors to the workplace.
Employee
The employee is expected to take reasonable care for their own health and safety and also the health and safety of others who may be affected by their actions. One of their obligations is to cooperate with their employer on health and safety matters and not to interfere with or misuse anything provided for their safety. Good management of health and safety can also save money.
Any person at a construction site, including workers and visitors, must take reasonable care of their own health and safety and that of others who may be affected by their actions or omissions.
The person must also comply with, so far as they are reasonably able, any reasonable instruction that is given by the PCBU to comply with the model WHS laws.
Benefits of meeting WHS requirements
Ensuring that you meet relevant work health and safety requirements will:
- improve worker morale leading to higher productivity
- improve work methods
- good public relations
- lower the incidence of workers' compensation claims
- minimise work stoppages due to safety disputes, investigation of incidents etc.
- reduce the possibility of action from Work Cover or Work Safe authorities.
- become an employer of choice
- create a safer community.
Not adhering by WHS regulations results in non-compliance and/or breach that may lead to serious sanctions, such as revoking, suspending or cancelling authorisations, infringement notices, or commencing prosecutions. Both corporations and individual workers may be prosecuted if found in breach of WHS regulations during a spot check. For example, a worker may be fined for not wearing appropriate personal protective equipment (PPE) provided by PCBU. Note, every State and Territory has different classes of fines.
Before commencing tasks, all foreseeable hazards (for example, falling off a roof, falling objects) and actual risks (e.g. death, serious injury) should be identified and appropriate safety measures put in place (e.g. install guard railing, prevent access under a roof being constructed). Control measures are selected by working through the 6 steps (or levels) of the Risk Control Hierarchy, from 1 to 6. Work sites often use the following structure to provide and maintain a safe work environment. The structure of the pyramid tells any person which control measure is most effective (in almost every situation), and which should be chosen first.
Level 1: Elimination
Eliminating the risks and hazards they create entirely is the most effective control.
Level 2: Substitution
Identify an alternative that does not involve or reduces the risks.
Level 3: Isolation
Isolate the risk to reduce it impact on people.
Level 4: Engineering controls
Adapt tools, equipment or engineering procedures to remove or reduce the risk.
Level 5: Administrative controls
Change work practices to minimise exposure to the risks or reduce the chance of injury.
Level 6: Personal Protective Equipment (PPE)
Use PPE to protect people from harm.
The Hierarchy of Control Measures
Some control measures are more effective than others. Control measures can be ranked from the highest level of protection and reliability to the lowest. This ranking is known as the hierarchy of control.
Eliminating the risk
This means removing the hazard or hazardous work practice from the workplace. This is the most effective control measure and must always be considered before anything else. For example, eliminate the risk of a fall from a height by doing the work at ground level.
If elimination of the risk is not reasonably practicable, you must consider using substitution, isolation or engineering controls, or a combination of these control measures, to minimise the risk.
Substitution
Minimise the risk by substituting or replacing a hazard or hazardous work practice with a less hazardous one.
For example:
- Substituting a manual task of carrying tools from one level to another with a material hoist or craning material will minimise the risk of workers developing a musculoskeletal disorder.
- Substituting a two-part epoxy substance with a water-based acrylic waterproofing system will minimise exposure to a hazardous substance.
- Substituting an ordinary brick-cutting saw blade with a noise-reduced saw blade will minimise exposure to hazardous noise.
Isolation
Minimise the risk by isolating or separating the hazard or hazardous work practice from people.
For example, isolating a mobile plant work zone from workers and/or the public with physical barriers will minimise the risk of contact occurring between a person and the mobile plant.
Engineering
Controls Engineering controls are physical control measures to minimise risk. For example, benching, battering or shoring the sides of the excavation will minimise the risk of a person being trapped and prevent the excavation from collapsing.
By enclosing an open cab excavator, for example, using a falling object protective structure (FOPS) or a roll-over protective structure (ROPS), will minimise the risk of an operator being struck by a falling object or being crushed if the excavator rolls over.
Administrative controls
Administrative controls should only be considered when other higher order control measures are not practicable, or to increase protection from the hazard. These are work methods or procedures that are designed to minimise the exposure to a hazard, such as ensuring there is no unauthorised entry of a person to a work area.
For example:
- Using a ‘keep out’ sign and a person to secure an exclusion zone when dismantling scaffolding to minimise the risk of people entering the work area and being struck by a falling object.
- Implementing a training program to show workers how to use new equipment.
- Implementing a job rotation system.
- Using permit systems to prevent unauthorised persons from entering a confined space.
Personal Protective Equipment (PPE)
Personal Protective Equipment (PPE) is the lowest order control measure in the hierarchy of controls. PPE should also only be considered when other higher order control measures are not reasonably practicable or to increase protection from the hazard.
PPE relies on the proper fit and use of the PPE and does nothing to change the hazard itself. It therefore requires thorough training and effective supervision to ensure compliance and effectiveness.
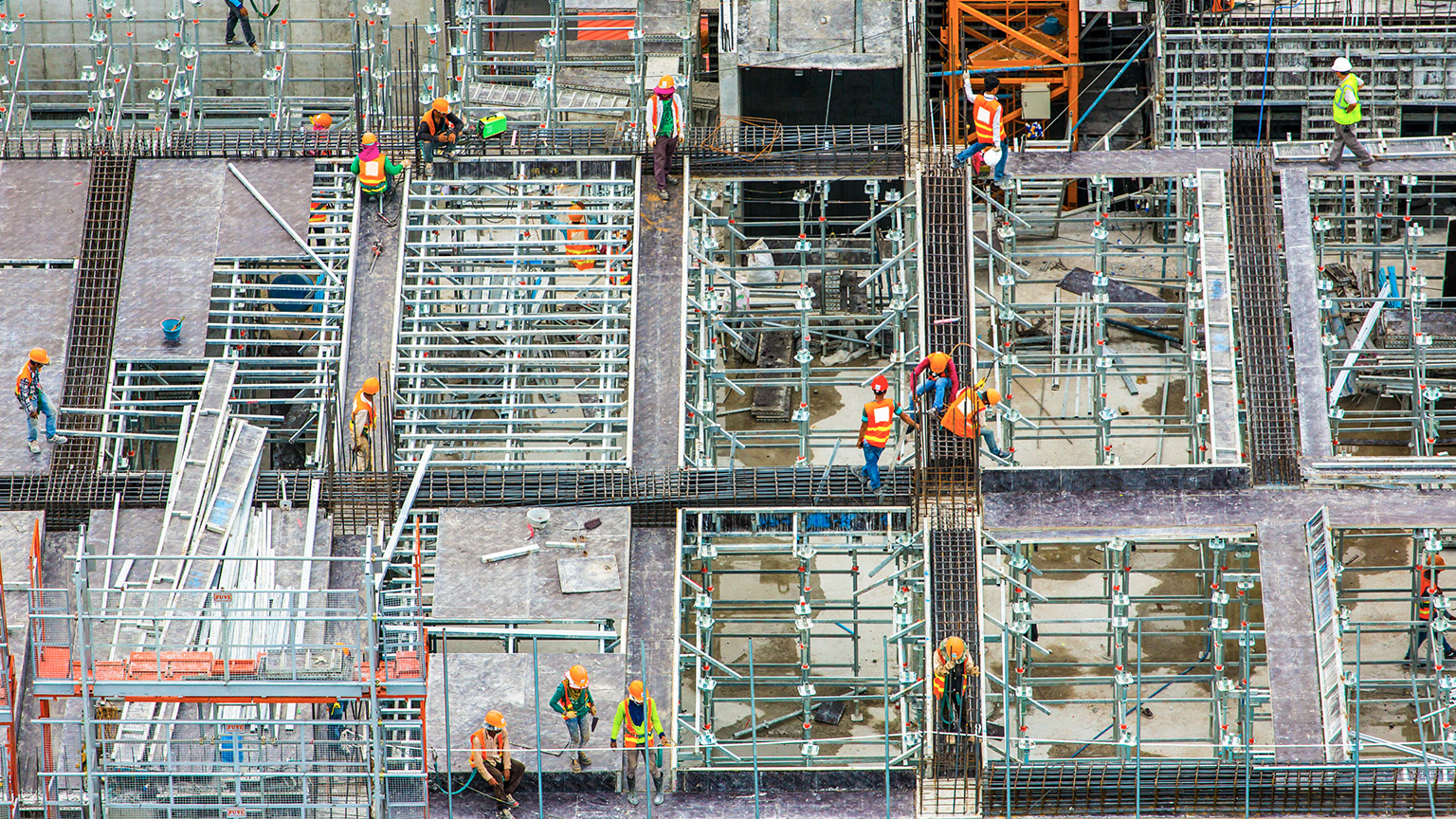