Lean methodology centres around the concept of efficiency. It arose from the Toyota production line in the 1950s. Lean is about maximising customer value using continuous improvement and eliminating as much waste as possible. 33
Waste is any human activity which absorbs resources but creates no value.James P. Womack and Daniel T. Jones, Lean Thinking32
Waste could be anything (time, money, resources, effort) that does not contribute to the value goal.
Lean is centred on preserving value with less work, with the ultimate goal of providing excellent value to the customer through a perfect value creation process that has zero waste.
This is done by empowering every worker to achieve their full potential and make the greatest possible contribution.
The goal of empowerment is based on the idea of showing respect for:
- The end customer
- The workers
- Suppliers
- Society.
Lean leaders facilitate this goal through problem-solving training. They help workers grow professionally and personally, allowing them to take pride in their work.
The Lean philosophy's heart is the concept of "kaizen", or continuous improvement. Continuous improvement aims to eliminate all waste in the value delivery process. 33
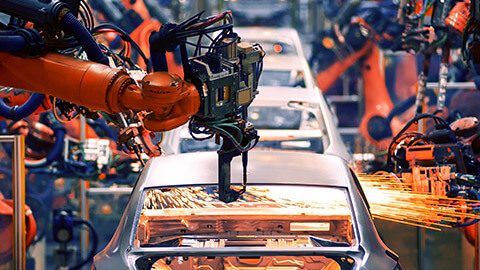
The Toyota Production System
Toyota collaborated with Taiichi Ohno to develop a new means of production. They found a way to make products faster, lower in cost, and higher in quality and variety.
Ohno faced the challenge of trading off between productivity and quality. His experiments led to the development several novel ideas that became known as the 'Toyota Production System'.
The Toyota Production System (TPS) was established based on two concepts:
- The first is called "Jidoka" (Japanese for "automation with a human touch"), which means that the equipment stops as soon as a problem arises, preventing faulty products from being produced.
- The second is the "Just-in-Time" concept, in which each process produces only what is needed by the next process in a continuous flow. 33
The Toyota Production System can efficiently make quality products that meet customer requirements based on these two philosophies. 33
James P. Womack, Daniel T. Jones and Daniel Roos first introduced the concept of Lean in their book, The Machine That Changed the World (1991), after observing many manufacturing systems including Toyota. The Lean Enterprise Institute summarised their findings as the following principles:
- Specify value from the standpoint of the end customer by product family.
- Identify all the steps in the value stream for each product family, eliminating, whenever possible those steps that do not create value.
- Make the value-creating steps occur in a tight sequence so the product will flow smoothly towards the customer.
- As flow is introduced, let customers pull value from the next upstream activity.
- As value is specified, value streams are identified, wasted steps are removed, and flow and pull are introduced; begin the process again and continue it until a state of perfection is reached in which excellent value is created with no waste. 33
Womack and Jones recommend that managers and executives embarking on lean transformations think about three things:
- Purpose: What customer problems will the business solve to be able to prosper?
- Process: How will the business assess each major value stream to make sure each step is valuable, capable, available, adequate, flexible, and that all the steps are linked by flow, pull, and leveling?
- People: How can the business ensure that every important process has someone responsible for continually evaluating that value stream in terms of business purpose and lean process? How can everyone touching the value stream be actively engaged in operating it correctly and continually improving it?
When developing a Lean organisation, it is important to align the purpose, process, and people. 33
Value stream
A value stream is the set of actions to add value to a customer from the initial request through realisation of value by the customer.
In a lean organisation problems are seen as opportunities for meaningful learning rather than errors to be swept under the rug.
Managers
Lean leaders also create and act as coaches and help others.
Lean is now widely recognised as a fundamental business philosophy applied across many organisations and industries. Organisations that consistently practice Lean are more innovative and competitive, which leads to higher profit and sustainability. 33
Muda is the Japanese word for waste. Seek it out and eliminate it!
The seven wastes of Lean Manufacturing are what we are aiming to remove from our processes. But what exactly are the seven wastes of Lean Manufacturing (or 7 Mudas)?34
One mnemonic you can use to remember these is: Who is TIM WOOD?
- Transport
- Inventory
- Motion
- Waiting
- Over-Processing
- Overproduction
- Defects
It is our goal to eliminates as many of these wastes as possible.34
Running a business
You are running a fast food restaurant that serves burgers.
This is a map of your store. You have three employees; Anita, Eric and Molly. Your business is not performing well and your employees are complaining that the process is inefficient. Currently a burger patty is fried by Anita, then must be taken over to Eric’s table to assemble the burger, then to Molly’s table who packages the orders and finally to the customer at the front desk.
Make a list of any improvements that you can think of to make that eliminate waste, or Muda; and which of the 7 wastes they each eliminate.
Share your answers in the forum with your peers.
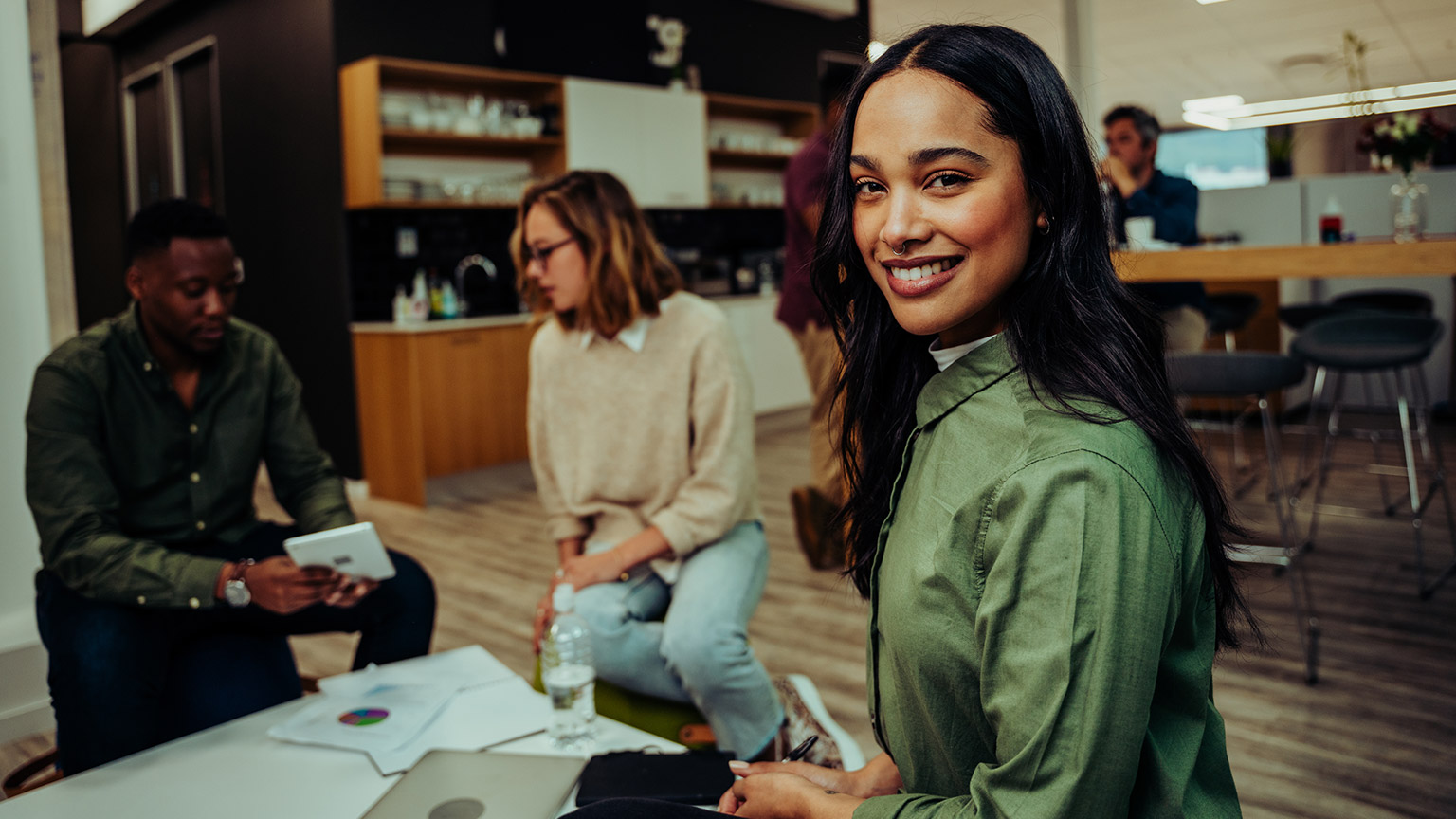