In this topic, we will discuss the principles and processes involved in managing project quality. Additionally, the roles and responsibilities of quality personnel are investigated, as well as the importance of identifying and collaborating with stakeholders.
By the end of this topic, you will understand:
- the time, quality, cost triangle
- the phases in the PQM process, including quality planning, assurance and control
- what is meant by a quality management system (QMS)
- personnel requirements for PQM
- PMBOK information for PQM
- what is meant by quality, quality management (QM) and total quality management (TQM)
- key points about modern theories of quality management.
~ William A. Foster 1“Quality is never an accident; it is always the result of high intention, sincere effort, intelligent direction, and skilful execution; it represents the wise choice of many alternatives.”
All projects are driven by three constraints that must be balanced.
These are:
- Time available time for production and delivery of the deliverables
- Resources and funding available for the project work
- Agreed quality or standard of the deliverables
The balancing of these constraints is called the scope triangle or quality triangle.
On many projects, one of these constraints may be fixed, while the other two fluctuate as the work progresses. Often the delivery time is fixed, and the quality of the deliverables will depend on the available funding and resources. If a specific level of quality is required, the cost will depend on how much time is available.
If two of the constraints are fixed, such as cost and time, the quality of the deliverables may need to be lower, or some features or functionality may need to be removed.
Watch
Quality Management – Introduction (7:50). Watch this YouTube video explaining the concept of quality and the link between quality, competitiveness and customer service:
Scope creep
Requirements for a project’s deliverables are usually agreed upon before the work begins. Scope creep occurs when these requirements change as the work progresses. For example, the client asks for additional functionality in an IT project.
There are several options for moving forward in this situation, including:
- Add more time: this will delay the delivery date and cost more for the extra work involved
- Add more resources: this may be extra team members, which, again, costs more
- Cut quality: this may mean lowering the overall standards for the whole project or removing some nice-to-have features
Experienced project managers can juggle time, cost and quality and make frequent decisions based on project progress reporting and input from the client, team members and other stakeholders.
Resource
Learn more about the cost or scope triangle.
Watch
How to Manage a Great Project – The Time-Cost-Quality Triangle (3:17). Watch this YouTube video describing this fundamental concept in project management:
There are three phases in the PQM process including:
- Quality planning
- Quality assurance
- Quality control
The following table summarises the activities and key documentation for each process:
PQM Phase | Example Activities | Key Documentation |
---|---|---|
Quality Planning | Developing:
|
|
Quality Assurance |
Carrying out:
|
|
Quality Control |
Carrying out:
|
|
Individual PQM phases are discussed in more detail in topics 2, 3 and 4.
Project management (PM), project time management (PTM) and project quality management (PQM) are separate processes. They overlap, but each has its own focus and type of work carried out.
Process | Focus Is On | Type of Work Carried Out |
---|---|---|
Project Management |
|
|
PTM |
|
|
PQM |
|
|
Inputs for the PQM Process
Inputs for the PQM process may include:
- Items from the project management plan:
- Project charter
- Scope statement
- Project objectives
- Work breakdown structure (WBS) and WBS dictionary
- Risk management plan
- Quality policy and quality objectives
- Other relevant policies and procedures
- Financial requirements for the project, including relevant accounting cost codes
- Relevant legislation and standards
- Lessons learned from other projects, including audit results, test plans and cases and data analysis
Large organisations may have a permanent quality team led by a quality manager. In smaller organisations, the project manager may perform PQM tasks assisted by assigned team members. Specialist consultants may also be engaged as a quality team or individually. It is important that you understand your organisation’s approach to carrying out PQM.
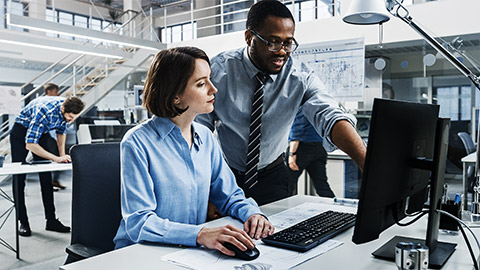
Resource
Project Quality Management, by Adobe Workfront, 2021
Project Quality Management – A Quick Guide, by Stephanie Ray, 2018
Watch
Tools and Techniques used in the Plan Quality Management process (8:12). Watch this YouTube video by PMC Lounge describing the tools and techniques used in planning PQM:
Quality Assurance (QA) and Quality Control (QC)
QA and QC are often used interchangeably, and some aspects of QA and QC activities are similar. QA is about managing quality throughout a project’s life cycle, while QC only verifies the quality of the deliverables.
The following diagram shows how QA and QC are both components of an organisation’s quality system, while QC is a component within QA:
The ISO 9000 standard defines both QA and QC as being part of quality management, but each has a different focus:
- QA: focuses on providing confidence that quality requirements will be fulfilled
- QC: focuses on fulfilling quality requirements2
Simply put, QA is a strategy of prevention, and QC is a strategy of detection.
The following table summarises the differences between QA and QC:
Quality assurance | Quality control |
---|---|
|
|
Both QA and QC are needed for project success:
- Using only QA provides a set of processes to follow to ensure quality in how the deliverables are produced, but the deliverables themselves are not tested
- Using only QC, the deliverables are tested for quality, but there is no process for repeating the tests, understanding and eliminating problems or making improvements.
Some quality system activities are not clearly defined as having a QA or QC focus or may involve both. This often depends on the size and complexity of the project and the industry involved. 4
Quality Management System (QMS) is the collective name for an organisation's activities, documentation and responsibilities to ensure the required quality of its products and services. A QMS also helps the organisation meet regulatory requirements and improve efficiency.
There may be variations in different QMSs across organisations and industries, but the following items are key requirements for any QMS:
- Quality policy and objectives
- Quality manual
- Quality management plan
- Procedures, instructions and records
- Processes for:
- managing data
- determining customer satisfaction and collecting customer feedback
- analysing quality data
- identifying opportunities for improvement.
ISO Quality Standards
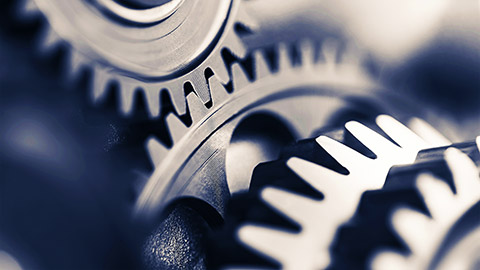
Purpose of standards
Standards provide a framework to assist organisations to establish processes and policies to deliver services and provide products.
Organisations may follow ISO standards which are international guidelines of best practice.
Standards are used to:
- help organisations provide products and services to meet the needs of customers
- aid organisations to consistently provide products and services to meet customer expectations
- assist organisations in complying with regulatory requirements
- streamline business processes
- increase business efficiency and reduces costs
- improve communication within the organisation
- improve its overall performance and competitiveness
ISO 9001:2015 Quality Management Systems is an international quality management system standard and benchmark that specifies the requirements for a quality management system when an organisation:
- needs to demonstrate its ability to consistently provide products and services that meet customer and applicable statutory and regulatory requirements, and
- aims to enhance customer satisfaction through the effective application of the system, including processes for improvement of the system and the assurance of conformity to customer and applicable statutory and regulatory requirements.
The following information about the standards is from SAI Global, where the standards can be purchased.
The standard consists of 10 clauses, which include all the components that make up the standard. Each section concentrates on the requirements involved in the aspect of the quality management system.
Clause 0 to 3 of ISO 9001:2015 describes requirements for a QMS, including process requirements and products and services requirements.
Clause 4 of ISO 9001:2015 describes how the organisation must understand the external and internal factors that may affect its ability to achieve the desired results.
Clause 5 of ISO 9001:2015 describes how the organisation’s leaders must commit to the success of the management system, providing sufficient resources, ensuring the quality policy and objectives are in place, and clearly communicating roles, responsibilities and authorities.
Clause 6 of ISO 9001:2015 describes how planning must address actions to address risks and opportunities; quality objectives and how to achieve them; and change management.
Clause 7 of the ISO 9001:2015 standard describes how the organisation must ensure sufficient resources are allocated to the quality management system, and carefully monitor their use and effectiveness.
Clause 8 of the standard describes how the organisation should plan, implement and control processes to meet requirements for providing its products and services.
Clause 9 of the ISO 9001:2015 standard describes how the organisation must be able to demonstrate and verify process capability as specified by the customer’s approval process requirements.
The final clause of ISO 9001 requires a commitment to continuous improvement, including managing nonconformities, solving problems, error-proofing, and taking corrective action when required.
Roles and responsibilities of quality management personnel
ISO 9001 quality management standards requires the organisation to demonstrate leadership and commitment to the QMS.
Role and responsibilities include:
- ensure quality policy and objectives are in place
- provide sufficient resources
- clearly communicate roles, responsibilities and authorities
Each employee must understand the QMS, quality policy and objectives and their role in contributing to quality within the organisation.
Clause 5.3 Organisational roles, responsibilities and authorities of the standards states top management shall assign the responsibility and authority for:
- ensuring the quality management system conforms to the requirements of this International Standard
- ensuring the processes for delivering their intended outputs;
- reporting on the performance of the quality management system and on opportunities for improvement, in particular to top management;
- ensuring the promotion of customer focus throughout the organisation;
- ensuring that the integrity of the quality management system is maintained when changes to the quality management system are planned and implemented.
Quality roles and responsibilities must be reflected and defined in the organisation’s QMP.
Watch
What is a Quality Management System? (3:51). Watch the following YouTube video by Best Practice:
ISO 9001 – Quality Management Systems (1:45). Watch the following YouTube video by TQCS International:
Reading
- You can find out more about what a QMS is
- You can find out more about ISO Standards
- You can find out more about the benefits of a QMS
Quality Policy and quality objectives
A quality policy describes the commitment of an organisation to comply with the requirements for making its products and services. The policy aligns with the organisation’s mission and vision and is available to all stakeholders. Many companies publish their quality policy on their website.
Quality objectives are the measurable goals that must be met to fulfil the quality policy. They can include goals for specific initiatives such as improving delivery times, reducing waste or reducing energy use.
Resources
- Find out more about the purpose of a quality policy and see an example policy: The purpose of a quality policy, by Kelly Huckabone, 2020
- How to Write a Good Quality Policy, by Mark Hammar, ISO 9001 Blog, 2014
- 16 Examples of a Quality Policy, by John Spacey, 2 July 2017
- 14 Examples of Quality Objectives, by John Spacey, 6 July 2017
Reading
Review the Nestlé company’s quality policy
Review your organisation’s quality policy. Note the differences and similarities between these two policies.
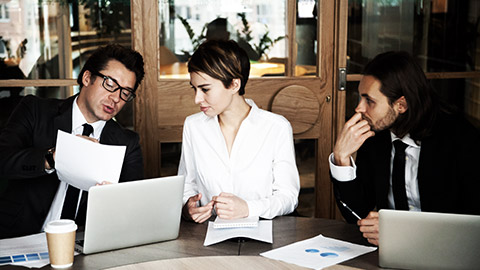
Quality manual
The quality manual describes the organisation’s QMS and how the organisation will achieve the requirements of relevant standards or requirements. Key items to include in the manual are:
- Quality policy
- Scope of the QMS: what is included in the QMS and what is not
- Quality processes: how key activities are to be carried out
- Management responsibility: senior management roles and responsibilities involved with the QMS
Other items may be included depending on the industry, organisation and project. These may include processes for maintaining premises and equipment, employee safety and control of documents and records. 5
Quality Management Plan (QMP)
A quality management plan (QMP) may also be called a project quality plan (PQP) or quality assurance plan (QAP). This plan is a component of the overall project plan and may be written by the project manager or quality manager. A QMP is a key deliverable from phase 1 of the quality management process, quality planning. More information about this plan and how to prepare it are given in chapter 2 of this learner guide.
Watch
Project Quality Plan: Project Management (5:06). Watch this YouTube video by Terrena Hooper providing guidance on developing a project quality plan:
Benefits of a QMS
Key benefits of a documented quality management system are meeting customer requirements, assisting the organisation with compliance and producing products and services in the most cost and resource-effective way.
Meeting customer requirements enhances confidence in the organisation and increases sales and consumer trust. Assisting with compliance increases trust in the organisation’s brand and its operations. Achieving more effective production and increased sales allows the organisation to grow and be more profitable.
Identify quality objectives and standards with input from stakeholders
The focus of project quality management is to ensure that products and services meet or exceed the needs of stakeholders. The project manager is responsible for identifying quality objectives and standards in consultation with the relevant stakeholders. It is critical that the project manager identifies the quality standards and objectives that are important to them. As we discussed previously, the time-cost triangle is an important consideration covering time, resources and agreed quality or standards of the deliverables.
Everyone within an organisation is responsible for ensuring that products or services meet quality management standards. Ongoing staff training and support are significant elements of any successful quality assurance program. After all, employees implement quality standards and ensure that they are met. Quality assurance systems fail when staff members are uncertain of their roles and responsibilities.
Quality outcomes require consistent performance. Therefore, ongoing staff training and support are critical aspects of quality management.
Depending on the size and structure of an organisation, quality control (QC) tasks may be carried out by different personnel than those who carry out quality assurance (QA) tasks. There may also be a quality team led by a quality manager.
On many projects, the project manager may share responsibility for PQM with the quality manager or a senior executive responsible for quality management.
Quality management requires teamwork to accomplish long-term goals and implement short-term initiatives within the organisation. Collaboration enables the improvement of processes, products, services and organisational culture.
More information about QA and QC tasks is given in topics 3 and 4 of this learner resource.
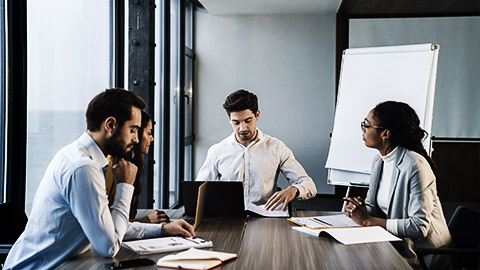
PMBOK stands for the Project Management Body of Knowledge. It contains internationally agreed processes, best practices, guidelines and terminologies for project management, grouped into ten knowledge areas.
Using PMBOK allows organisations to standardise project management practices across departments and divisions. PMBOK supports project management careers and skill development by giving project managers a standardised system across companies and countries.
Project quality management (PQM) is the fifth knowledge area within PMBOK. Information and processes are provided for the three PQM processes, including inputs and outputs, tools and techniques for each.
PMBOK definition of quality and grade
PMBOK defines quality and grade as two different things:
- Quality: the degree to which a set of inherent characteristics fulfil requirements
- Grade: the performance specification to which a product is produced
A product may be high-grade because it has many features, but its quality may be poor if some of those features do not work. For example, a software application with an extensive range of functions may be sold as a high-grade product, but its quality will be poor if some functionality does not work. Similarly, a product sold as a lower-grade product with fewer functions may be of high quality if it performs well.
It is important to understand the required quality and grade for project deliverables at the start of the project. It is possible and reasonable to offer a quality, low-grade product if the organisation intends this. However, having a low-quality product of either grade is not good business practice.
Resource
- What Is PMBOK in Project Management? Understanding PMBOK Methodology
- Project Quality Management According to the PMBOK, by Bernie Roseke (2018)
Quality refers to the characteristics of a product or service that enable it to meet or exceed customer requirements. Achieving high quality is a continuous process.
Quality management (QM) reinforces the need to improve quality constantly. Quality management involves every aspect of an organisation or business, including processes, environment and people. Total quality management (TQM) requires everyone, from senior management to team members and production workers, to commit to improving quality.
Quality and TQM are about managing the total production process to produce a quality product or service. Every aspect of our lives depends on these concepts being carried out successfully, from our food to the cars we drive, our schools and medical facilities, buildings, transport and roads.
Older management methods focused on the production volume and the cost of making a product. Quality was controlled by inspecting batches of finished products and accepting a specified amount of rejects, returns or complaints. Management’s role was seen as assigning work, controlling production and solving problems. Lapses in quality were fixed by replacing products or changing processes in response to each lapse.
Total Quality Management, or TQM, is a business philosophy that emphasises the continuous improvement of products and services to provide the best possible customer experience. TQM practitioners believe every employee has a role to play in improving the quality of the company's products and services.
TQM is built on the foundation of four principles:
- quality comes first
- customers are always right
- employees are the key to success
- continuous improvement is essential.
These principles guide businesses in their quest to provide their customers with the best possible products and services.
TQM has been shown to be an effective way to improve quality and customer satisfaction. In fact, many companies who have adopted TQM report increased sales, higher profits, and happier employees.
Case Study
Quality in Japan and the USA after World War II
After the Second World War, the USA had a high demand for goods and products. Manufacturers sold everything they made. Businesses concentrated on increasing production rather than controlling quality. They thought they could sell anything and that customers were not interested in quality.
In Japan, the situation was different. The country was devastated and needed to rebuild production capability. Manufacturers had to battle the perception that their products were low quality. Japan focused on quality improvement and learning from foreign experts. After twenty years of effort, their high-level managers were leaders. Everyone was trained in managing quality and continuous improvement. By the early 1980s, the quality of Japanese products, such as cars and electronics, was higher than that of US-made products.
Resource
Learn more about quality, TQM and the pioneering quality experts who drove these changes.
There are several QM methods in use today. These incorporate the concept of continual improvement with quality planning, assurance and control activities to give four essential elements of quality. As a professional responsible for managing and leading a project, it will help you understand key information about these methods, including how, when and why each is used.
Here is a summary of some of these best-known modern QM methods:
- Kaizen: A process of small continuous improvements for significant growth with a focus on teamwork, personal discipline, improved morale, quality circles and suggestions for improvement
- Zero Defect Programs: A preventative tool that always reduces defects by performing every job to an exceptional standard
- Six Sigma: A data-driven review process that improves business processes by limiting the probability of errors. The aim of the six sigma is to identify and remove the causes of defects and minimise impact variability in manufacturing and business processes to ensure a quality, consistent product or service. Therefore, the outcome is a quality assured process or product.
- Quality Circle: A participation management technique where a team regularly meets to identify, analyse and solve work-related problems
- Taguchi Methods: A robust design method where statistics are used for quality improvement
- Kanban: A lean management method to balance capacity and improve workflow within production systems
- Kansei Engineering: A tool that supports future product design by translating customer feelings into product parameters
- TRIZ: Also known as the Theory of Inventive Problem Solving; an innovative technique to gather data on similar projects to inform best practice
- Object-Related Quality and Risk Management (OQRM): A method to control risk and quality
- Top-Down and Bottom-Up Design: Strategies to process information and order knowledge; often applied in thinking, teaching and leadership
Case Study
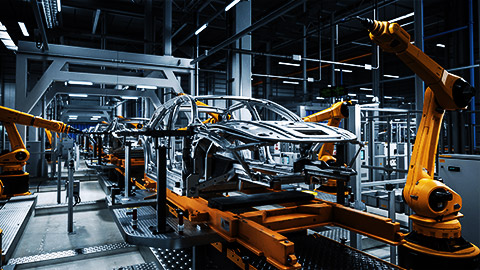
Toyota – Excellence in Quality Management
Toyota is an example of excellence in quality management. Taiichi Ohno, an industrial engineer at Toyota, implemented the Kanban system to manage and control the efficiency of the manufacturing process. It acts as a just-in-time (JIT) inventory process to minimise loss. Considered a ‘lean tool,’ Kanban enabled Toyota to produce the appropriate number of parts when they were needed in production. Today, innovators such as Pixar Studios use the Kanban system in their daily operations.
Toyota’s Six Kanban Rules:
- Never pass on defective products
- Take only what is needed
- Produce the exact quantity required
- Level the production
- Fine-tune production
- Stabilise and rationalise the process
Website
Find out more about Toyota’s Kanban rules
Video
Watch the video How Toyota Changed the Way We Make Things (4:37) using a Kanban system in production.
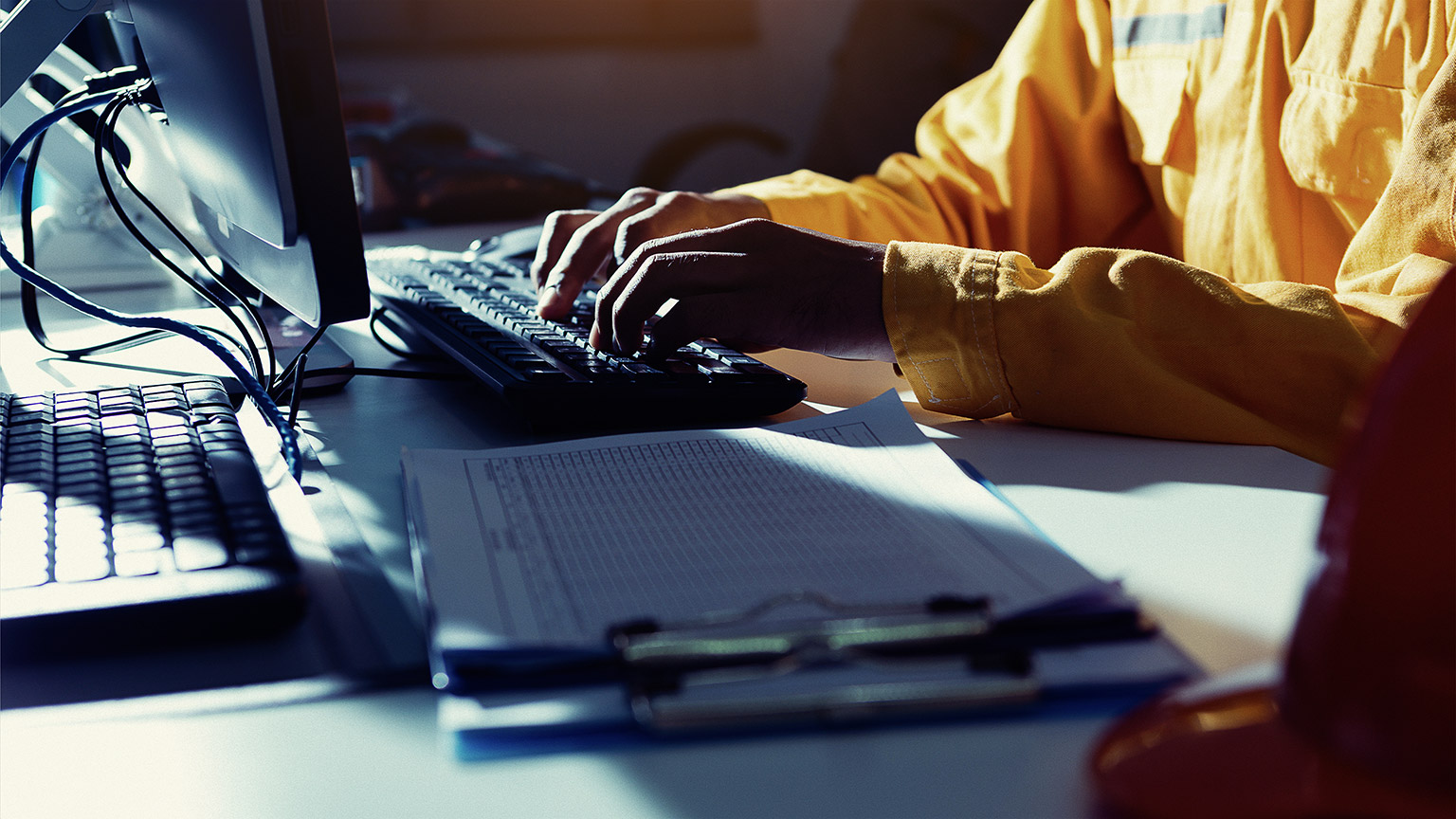